Choosing the right cobot gripper for cosmetics handling
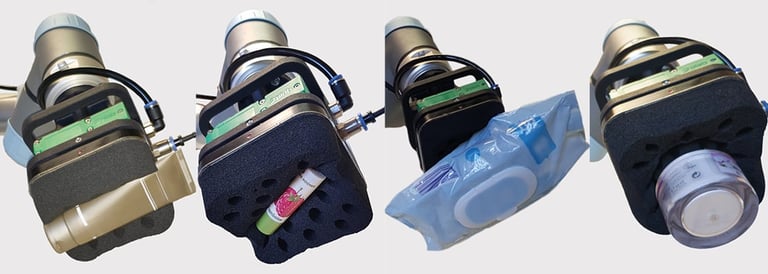
For the cosmetics industry, placing products into packages aimed at a wide variety of different channel partners, ranging from huge divisions in department stores or flagship outlets to tiny cosmetic shops, is a particular challenge. Today this task is often fulfilled by an armada of workers hand picking and placing each item into each specific box. The opportunity for automation seems obvious, but it is also challenging as it demands an extremely high degree of flexibility to make an investment economically worthwhile. The UR Plus certified Kenos® KCS gripper from Piab, addresses this issue for customers from the cosmetics industry who need a solution to provide many small items combined in various ways for different store types.
Universal Robots, a pioneer and innovator in the development of cobots for the manufacturing industry, is a specialist when it comes to providing automation solutions that solve tasks collaboratively with the human workforce. While easy to use and fast to deploy, flexibility often depends on the gripper technology. To support Universal Robots vision of providing an “out-of-the-box” usable solution, the gripper must seamlessly integrate into the UR Plus plug and play platform, which allows easy installation and implementations. The start-up phase of grippers certified for the UR Plus program is tremendously reduced by the requirement of Universal Robots that the gripper manufacturer provides socalled UR Caps. These are small programs similar to mobile phone apps and enable the user to commission a new gripper on a Universal Cobot without detailed programming know-how within a few minutes. Piab’s Kenos® KCS gripper is now equipped with the respective UR Cap and listed on the respective UR Plus Solutions website. Any gripper used in cosmetics distribution needs to offer the flexibility of being able to handle all kinds of products in every shape and packaging type, be it cartons, bags, tubes or glass containers.
Particularly in the cosmetics industry with its high mix of many different small products customers depend on flexible automation solutions that can handle whatever comes in front of them to make the investment worthwhile. With the flexibility of the Kenos® KCS gripper from Piab, customers in the cosmetics industry are able to pick and place products with any shape or surface making it easy for them to handle multiple different parts with just one end-of-arm-tool.
Piab's Kenos® KCS gripper consists of a separate pump unit that integrates modular vacuum generation in the smallest of spaces and of a gripper unit. Both are connected by a quick-change system. The main gripper consists of a technical foam, which can adapt to a wide variety of contours and can thus accommodate different parts flexibly. This eliminates in many cases the need for accurate identification of a workpiece as well as the gripping surfaces. Accordingly, in many applications, a change of the gripper when changing the parts to be handled is not necessary. The cobot is therefore ready for immediate use for different processes. In addition to the greatest possible flexibility in the field of application, time and cost savings are achieved through shorter downtimes and time needed for retooling. This is also contributed to by the fact that when the foam layer is worn, it can simply be exchanged, without replacing the entire gripper. For direct handling of food, the gripper can also be equipped with a special FDA-approved technical foam. For special applications, such as the handling of plastic bags of concentrates or granulates, Piab has developed another gripper unit, which can be swiftly exchanged via the quick-change system.
Flexibility in terms of forms and surfaces that can be handled, as well as in the placement of products to be handled, are a plus for the cosmetics industry. For the Kenos® KCS gripper from Piab it does not matter if a product is placed exactly in a specifically planned location – it can pick it up as long as its surfaces gets a hold of it on most of the product.
The gripper units are characterized by their edgeless design. Due to the rounded sides and the surface of technical foam, possible injury hazards were largely eliminated. This makes the gripper units particularly safe to use on cobots, which cooperate freely with humans.
The pump unit is equipped with Piab's powerful new generation COAX® SX vacuum technology. The lightweight piCHIP unit is a small, integration-optimized vacuum pump and was selected because of its almost silent operation, making it ideal for use directly next to the operator. Because COAX® ejectors are up to twice as fast as other ejectors and deliver three times more flow than a conventional ejector with identical air consumption, the piCHIP unit can deliver high performance even with low or fluctuating supply pressure. Independent comparison tests at the Fraunhofer Institute for Machine Tools and Forming Technology IWU in Dresden have shown that the Piab ejectors require significantly lower compressed air to achieve the same output compared to ejectors from other manufacturers. This makes them particularly energy efficient. Accordingly, their use reduces the cost of providing compressed air and thus the total cost of production. This is another important factor in increasingly competitive industries, especially as the handling and placement of a product is not itself a value-adding factor in production.