- News
- System integrator Umbra Control chose Piab's Kenos® KCS gripper
Absolute precision in the handling of thermoforms, with sealing rings, and their transport supports
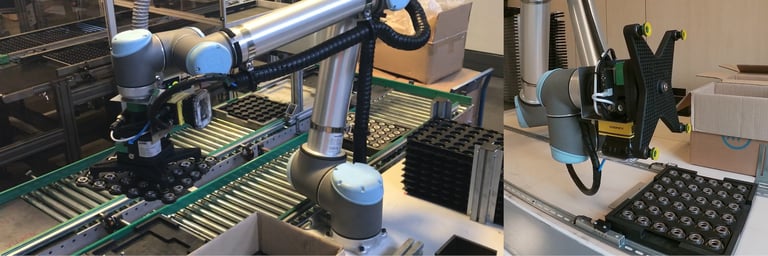
System integrator Umbra Control chose Piab's Kenos® KCS gripper, in a special version with four suction cups, to accurately and efficiently handle Meccanotecnica Umbra's end-of-line pick and place operations for the production of seals for the automotive industry.
Umbra Control deployed a Kenos® KCS gripping system on a collaborative robot installed on an assembly line at its customer Meccanotecnica Umbra SpA,. Before automating the process, the work was done manually by an operator. Today, the process is carried out by the UR10 cobot from Universal Robot, which uses the Piab gripper to handle thermoformed molds and trays containing sealing rings. The thermoform mold with the sealing rings lying in the respective cavities arrives at the end of the line on a conveyor belt and is detected by photocells.
The cobot is positioned so that the camera can frame the mold and check all the components in the cavities. During this phase, the unique codes of the sealing rings are read through the video analysis system integrated by Umbra Control in the UR10. The information is shown on the touch screen for the operator of the cobot to check. , Together with the new offline voice command system the touch screen represents the control interface of the entire system.
The cobot picks up the thermoformed mold with the controlled sealing rings and places it in the box to be filled. Thereafter, it picks up the empty tray underneath and places it on the starting point of the conveyor belt. Finally, the cobot picks up an empty thermoform mold from the racks at the beginning of the line and places it on the tray at the start of the conveyor.
The cobot repeats this cycle until it fills a box consisting of 12 thermoformed mold with 36 sealing rings each, then inserts an interlayer and completes the box before closing it. The process involves a cycle time of around 100 seconds for loading a single thermoform mold, giving a total of 15 - 20 minutes per box. What is important in this process step is not the speed, but the level of accuracy, as Meccanotecnica Umbra works with a zero error margin.
"The main issue was to find a reliable gripping solution for two types of surfaces: the thermoform mold containing the sealing rings and the tray that carries it," says Giorgio Passeri, Umbra Control's Software Research and Development Manager leading the project. "The plastic thermoformed mold has a geometry that does not guarantee high flexural rigidity. This significantly influenced the choice of gripper. Initially, systems simulating the action of the fingers of a hand and commercial end effectors with suction cups were evaluated. These were discarded because the thermoformed molds buckled in the outer areas. It was therefore necessary to develop a customized gripper, which we made together with Piab.
The choice fell on the Kenos® KCS system, the customization of which led to the distancing of the suction cups from their position in the commercial end effectors, allowing the thermoformed molds to be lifted in the outermost part, avoiding bending of the material. We started with a solution with 5 suction cups. However, during the tests not all 5 suction cups were able to grip efficiently, causing flexing of the thermoplastic. Therefore, we removed the central suction cup.
The vacuum channels feeding the suction cups located at the four corners of the end effector were longer than the channel feeding the central suction cup. This difference in length meant that the gripping at the central point took place earlier than at the perimeter, resulting in a deformation of the thermoformed material that prevented the perimeter cups from having an efficient grip. The solution with 4 suction cups solved all these problems. This also proved to be optimal for the tray, which has a regular surface and greater flexural rigidity than the thermoformed mold material," adds Giorgio Passeri.
"The correct functioning of the gripper is guaranteed by the COAX® vacuum generator from Piab, which is integrated into the Kenos® KCS gripper. A key feature of the pump is its counter-blow function, which promotes the release of the thermoform mold and the interlayer. Without this function, it would not be possible to detach the suction cups when the vacuum supply stops. The Piab solution we have chosen is certainly very competitive from an economic point of view, taking into account the consulting service that the technicians of the Italian subsidiary have offered us, in collaboration with Mateg, Piab’s authorized distributor, guiding us in the best possible way in our choice," concludes Giorgio Passeri.
Piab's Kenos® vacuum grippers are developed to simplify handling processes in a variety of industrial applications. The Kenos® KCS gripper was developed specifically for cobots. It is a plug-and-play system consisting of a compact, modular vacuum generator and a gripper, which in the standard version is made of a technical foam that can adapt to a wide variety of surfaces. Piab is also able to design and build customized systems, as was the case with Umbra Control.
Piab's COAX® vacuum generation technology minimizes energy consumption while offering a safe and fast grip, thanks to its high initial flow rate. The pump unit can deliver high performance even with low or fluctuating supply pressure.