
Chemical Manufacturing
In the rapidly evolving field of chemical manufacturing, process efficiency and safety are of extreme importance. With the increasing complexity of chemical formulations and the stringent regulatory environment, manufacturers are looking for advanced solutions that ensure seamless operations without compromising quality. Piab offers specialized vacuum conveying solutions customized for the unique requirements of chemical production.
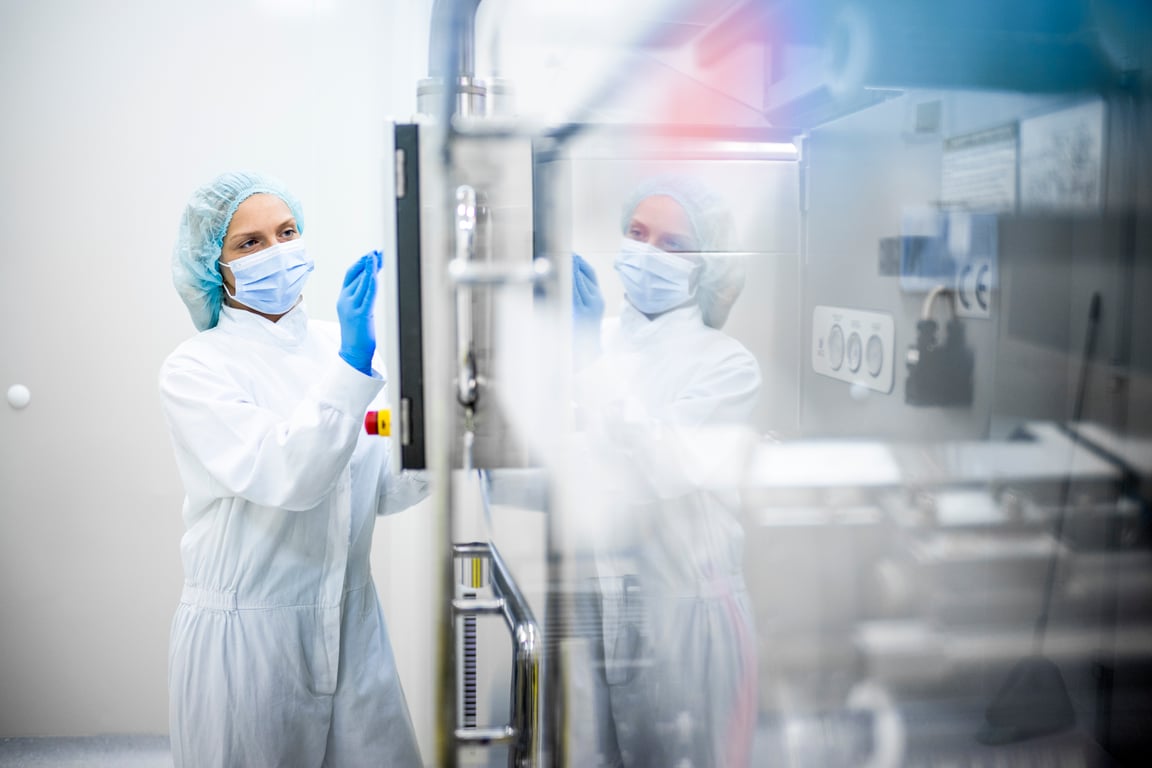
Challenges of chemical manufacturing
The chemical manufacturing sector faces numerous challenges that can affect productivity and efficiency. Especially the variety of materials and formulations can lead to different processing requirements, requiring highly adaptable equipment. The handling of hazardous materials poses significant safety risks, including exposure to toxic substances and the danger of spills and leaks during production. Also stricter regulations regarding safety and environmental impact need manufacturers to implement robust systems that ensure compliance at every stage of production.
Integrating Piab’s vacuum technology to address these challenges can help manufacturers aiming to sustain competitive advantage while maintaining high standards of safety and efficiency.
Piab vacuum conveyors in the chemical manufacturing processes
Elevate the detergent production line
Piab specializes in the transport of enzymes and enzyme-containing mixed powders with speed controlled dense-phase conveying. This method optimizes transfer speed without damaging the delicate enzymes.
Enzymes play a crucial role in modern detergent formulations, acting as proteins that catalyze chemical reactions to effectively break down soils and stains, thereby enhancing washing performance.
However, inhalation of enzyme dust or aerosols can lead to respiratory allergies. To reduce dust exposure, enzymes are transported in a closed system to minimize risks of contamination and ensure employee safety. Use Piab’s high efficiency ULPA filters to ensure the highest level of air cleanliness. Not only enzymes, but other powdered or granulated ingredients can be conveyed with Piab vacuum conveyors, as well as the finalized tablets.
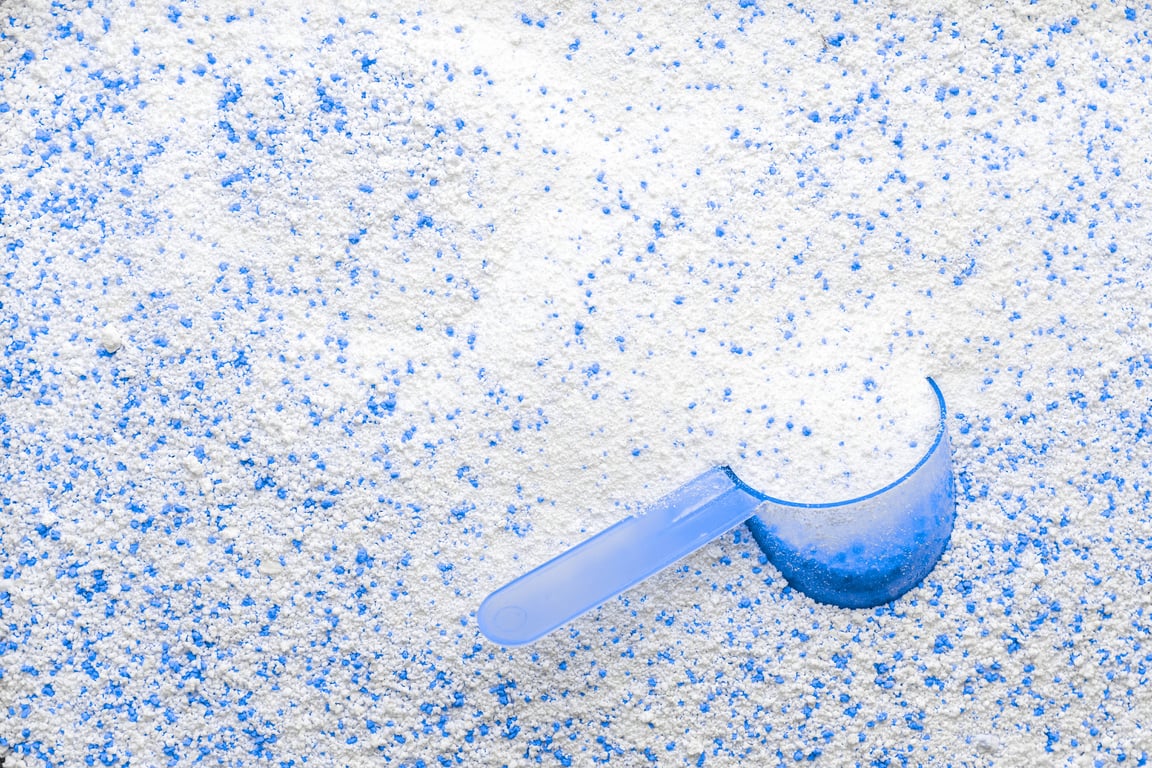
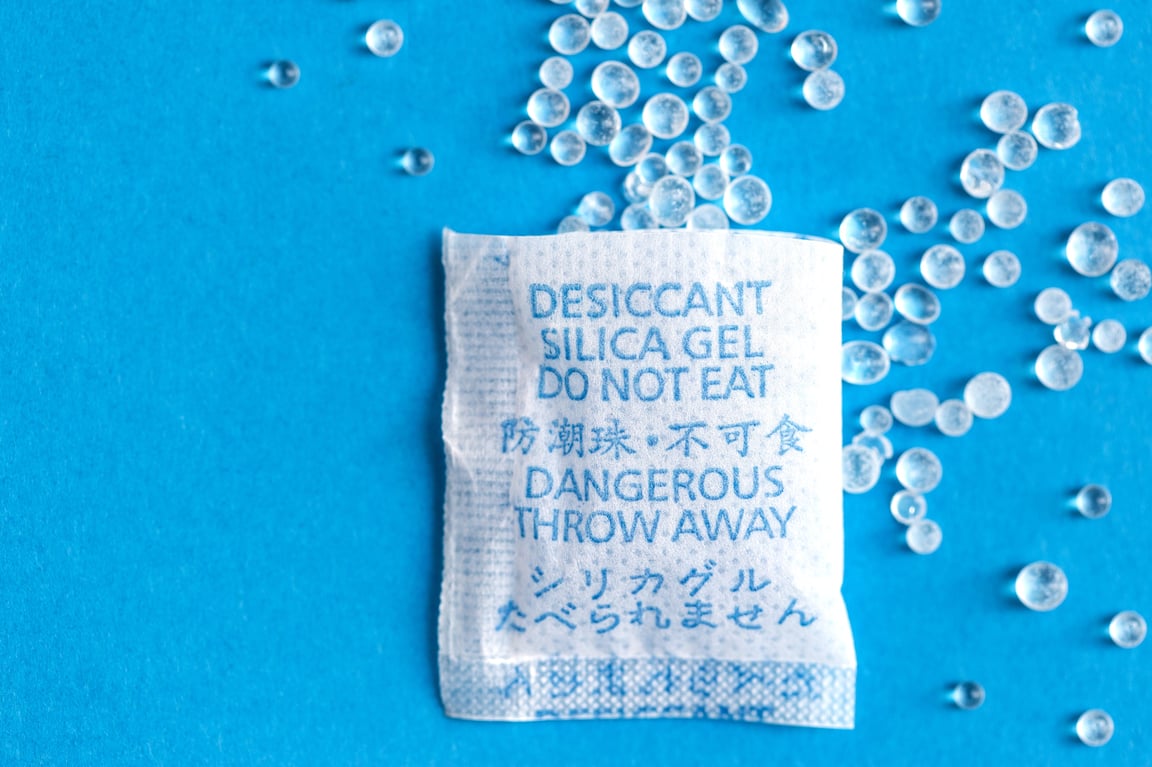
Desiccants manufacturing and silica gel conveying
The Desiccant manufacturing market serves global end-users in the food, pharma, consumer goods, and electronics markets. Desiccants are used to absorb moisture/water in order to keep products dry and protect from moisture/humidity.
Piab’s enclosed vacuum conveying system is used primarily in the packaging process of dessicants when the sachets are filled.
Supporting industrial water treatment systems
In water treatment, various chemicals are used to purify water by removing or neutralizing impurities, contaminants, and microorganisms. You can automate parts of your process if you handle the following materials:
- Alum (Aluminum Sulfate) - Used as a coagulant to remove suspended particles by causing them to clump together.
- Calcium Hypochlorite - Used for disinfection and to eliminate bacteria and algae.
- Ferric Chloride - Another coagulant used to remove suspended solids and phosphates.
- Sodium Bicarbonate - Used for pH adjustment and alkalinity control.
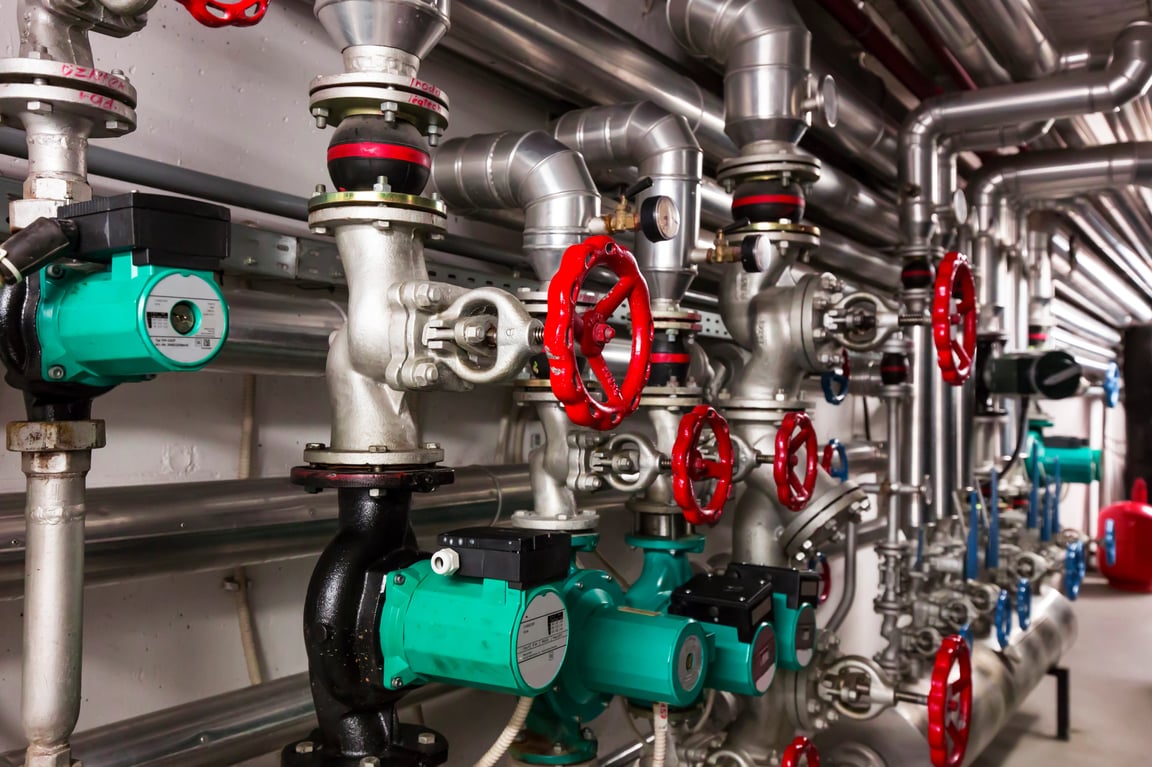
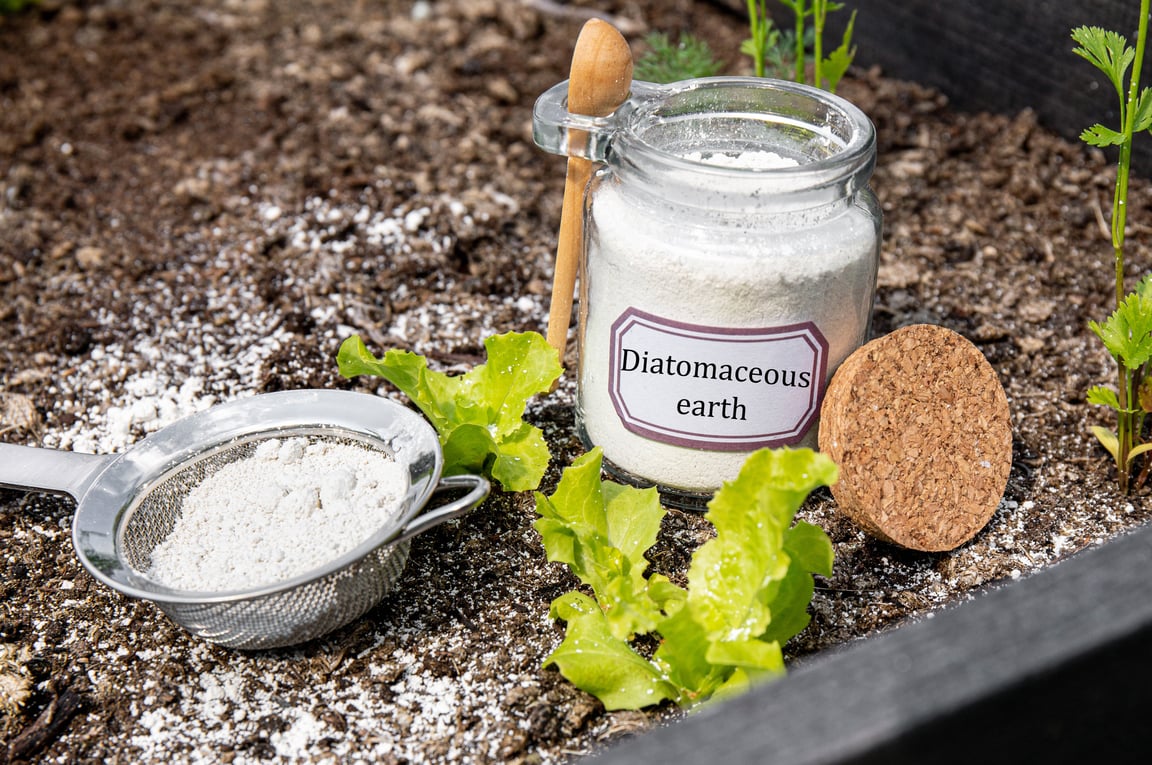
Handling Diatomaceous Earth
In pest control, Diatomaceous Earth is used as a natural pesticide, but it is also used in filtration systems, among other areas and industries. The lightweight particles of Diatomaceous Earth flow easily, and the closed system of Piab vacuum conveyors enhances workplace safety by minimizing exposure to its dust.
Gentle conveying of other powders, granules, and small parts
Other materials conveyed while producing chemical products include acid, sodium formate, and sodium chlorate, which are commonly fed into mixers and blenders.
Any free-flowing powders and granules are best conveyed with vacuum conveyors! A few examples where Piab conveyors have shown their merits are chlorine, polyvinyl alcohol, magnesium hydroxide, lime, pigments, activated carbon, carbon black, and fertilizer, among others.
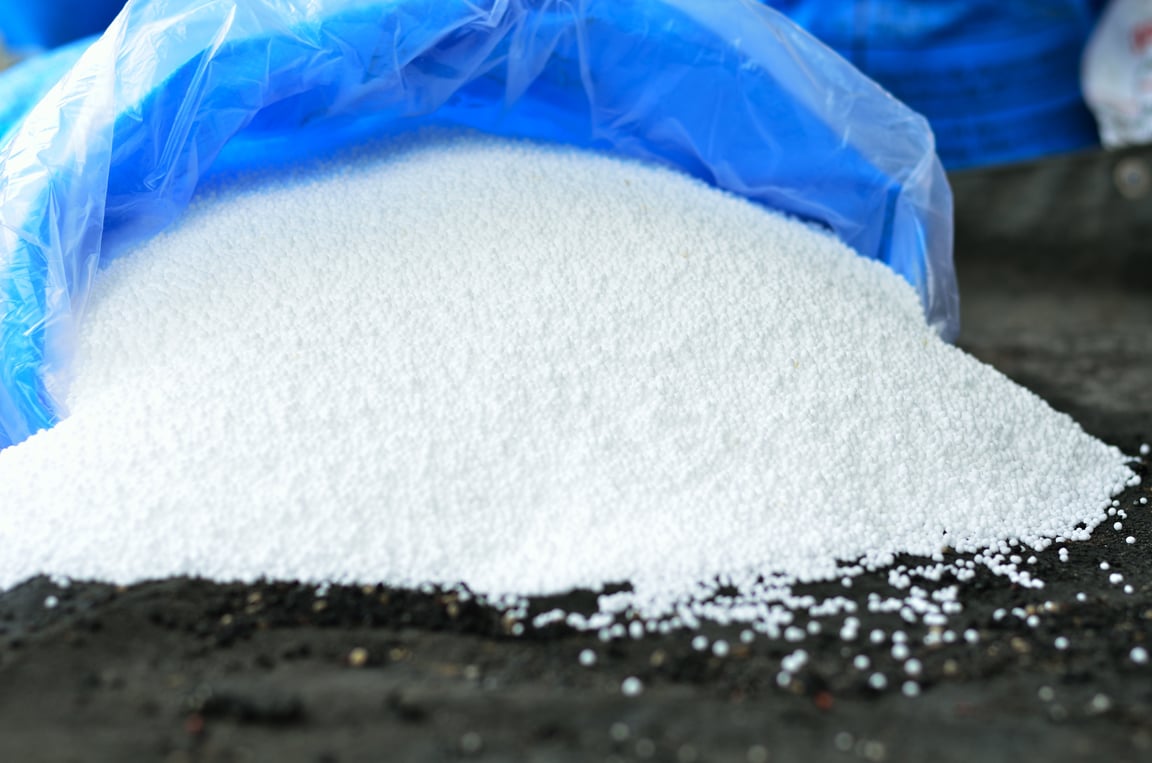
Ensuring a safe work environment with Piab’s vacuum conveyors for chemical manufacturing
Typical applications where Piab’s vacuum conveyors are installed within the chemical manufacturing process are to feed blenders and mixers with powdered ingredients and additives. They also feed reactors and holding tanks, and can also feed packaging machines with the finished product, compactors (tablet presses) with the detergent powder, and finally product reclaim from packaging and tableting processes to reduce the possibility of spills.
Filling tanks and reactors often release vapor which affects the conveyed powdered materials. Piab’s solutions minimize the effect of the steams/vapors and thanks to their closed design, the moisture can’t rise up into the conveying unit.
Benefits of conveying chemicals with Piab
Piabs vacuum conveying systems offer a versatile and efficient solution to several challenges in chemical manufacturing, ensuring safer operations and higher product quality.
Enclosed system for higher safety
Piab’s chemical conveyors are designed as a closed system. Utilizing a closed-loop design effectively minimizes contact with the external environment, significantly lowering contamination risks.
Enhanced efficiency
By streamlining the conveying process, Piab enables chemical manufacturers to optimize workflow, resulting in increased productivity and reduced downtime.
Suitable for various applications
Piab’s solutions are adaptable across various applications within the chemical industry, accommodating a wide range of chemical materials and formulations.
What customers say about our vacuum conveyors for chemical production
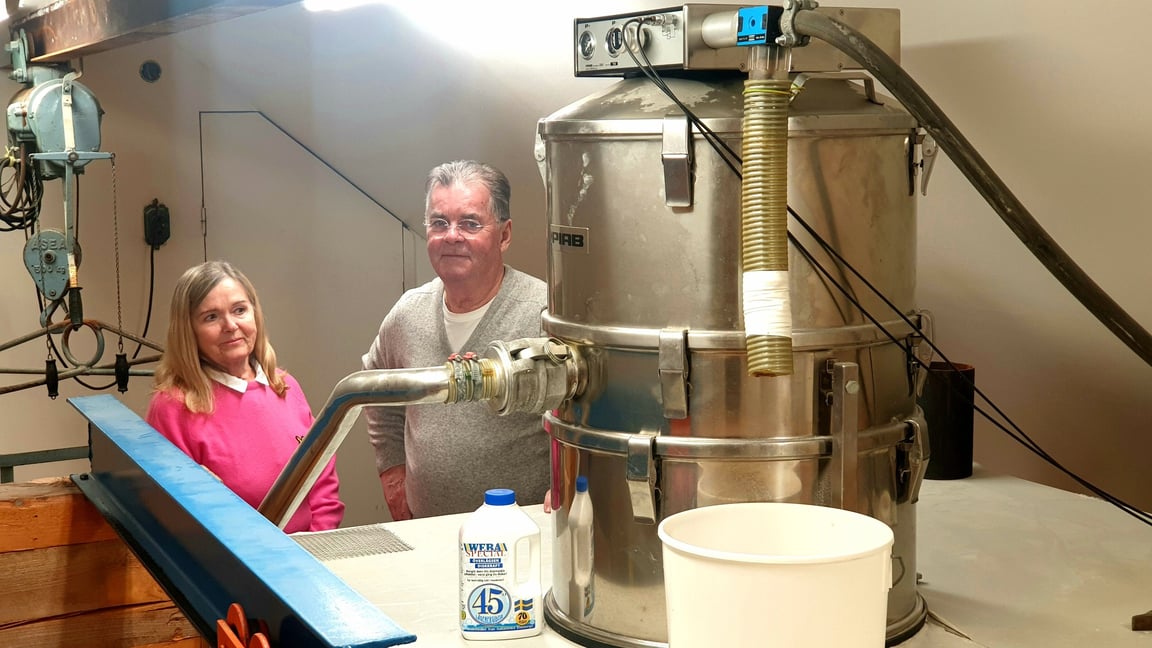
To move powder in an operation line is connected to great, potential danger since electrical impulses can cause dust explosions if something goes wrong. Piab offered the only solution based on vacuum instead of electricity, so once we found them, it was an easy decision to make.
FAQ
Piab's vacuum conveyors are designed with an enclosed system that minimizes the risk of contamination and exposure to hazardous materials. They are adaptable to various chemical materials and formulations, ensuring safe and efficient operations.
Our conveyors utilize a closed-loop design that significantly reduces contact with the external environment, lowering contamination risks. Additionally, they can be equipped with a high efficiency ULPA filter (U16 classed) to ensure the highest level of air cleanliness, protecting employees from hazardous dust exposure.
Yes, with Piab's accessories at the enzyme pick up point we can optimize the velocity of the enzymes. Piab's vacuum conveyors are equipped with speed-controlled dense-phase conveying technology, which optimizes transfer speed without damaging delicate materials such as enzymes. This ensures that sensitive ingredients maintain their integrity throughout the process.
Piab's vacuum conveyors can handle a wide range of materials, including enzymes, acids, sodium formate, sodium chlorate, and other powdered or granulated ingredients. They are also suitable for transfering finalized tablets and other chemical products.
By streamlining the conveying process, Piab's vacuum conveyors optimize workflow, leading to increased productivity and reduced downtime. Their adaptable design allows them to integrate seamlessly into various stages of chemical manufacturing.
Handling Diatomaceous Earth (DE) requires specific considerations due to its nature as a free-flowing powder. It is essential to use a system designed for fine powders, ensuring proper sealing and incorporating high-efficiency filters to capture fine particles effectively. Regular cleaning and maintenance of these filters are crucial to prevent clogging and maintain system efficiency. Given Diatomaceous Earth’s abrasive properties, employing wear-resistant materials for pipelines and components is advisable to ensure durability. Additionally, to prevent dust explosions, the system should be properly grounded to avoid static discharge, and using explosion-proof equipment may be necessary. Lastly, as Diatomaceous Earth can pose respiratory hazards, it is important to ensure the system is well-sealed and that exhaust air is adequately filtered to minimize exposure. Contact our experts to learn more about applications related to Diatomaceous Earth.
Get help choosing your ideal conveying equipment!
Find out what applies to your raw materials and products! Fill in the form to get free, personal advice from our engineers as well as comparisons with other technologies to find the best solution for your needs.