Automated powder handling with Piab’s vacuum conveyors ensures social distancing
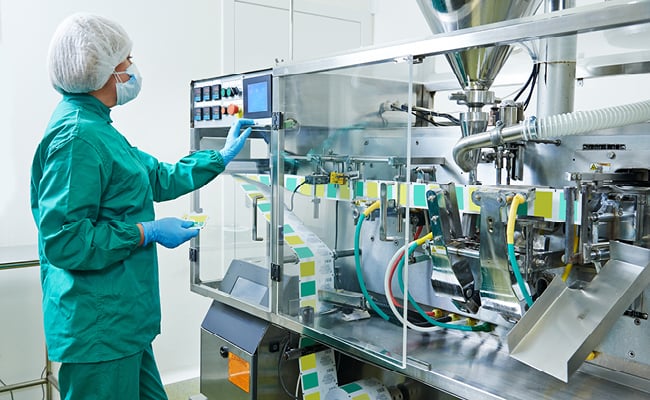
The second wave of seemingly stronger infectious COVID-19 mutations demand adhering to social distancing rules even more strictly than before. Here, automating material handling with vacuum conveying can play a major role in reducing contacts between employees, thus minimising the risk of contagion while maintaining productivity at a high level. This is particularly important in system relevant industries such as pharmaceuticals or food.
Pharmaceutical and food products are life essential and independent of lockdowns or mutating viruses. They must keep coming off the line and being delivered to consumers. At the same time companies need to avoid contagion between employees as much as possible to prevent personal related down-times. Therefore, many companies have already established shift work and determined necessary distances between operators. However, manual handling of ingredients is still widely spread especially when it comes to feeding mixers or tablet presses. As several employees are needed to keep the processes running, it increases the risk or forces companies to reduce productivity if left with just a few operators to ensure that social distancing can be maintained.
Automating powder and bulk handling processes by the deployment of vacuum conveyors enables social distancing while maintaining high productivity by reducing the need for numerous operators on one hand and the need for movement across the whole factory floor on the other. At the same time, it also improves ergonomics as operators no longer need to carry heavy buckets or bags up the stairs to feed funnels or hoppers. The vacuum conveyor can easily do so from a central material storage area. With Piab’s piFLOW® series conveyors that are easily cleaned, using the same conveyor is even an option for several ingredients.
Assuming nutraceutical tablet production, the manual feeding process often does not end at filling the powdered ingredients but continues at the tablet press. From here the tablets need to be fed for instance to a coating machine and ultimately to a packaging station - be it for individual blister or bulk packaging. In the worst case, an operator needs to continue picking up the tablets ejected from the press and manually bring them over to the next line and fill them into another funnel or hopper for further processing and packaging. This implies that he or she continues walking the floor and might meet other operators risking contagion, besides the unergonomic work conditions that can lead to back injuries.
Adding vacuum conveyors to automate each of the filling processes by connecting the separate steps, the production can run more smoothly. Or even become operator independent with Piab’s piFLOW®p SMART system further reducing the risk of lower production productivity or even downtimes caused by social distancing or missing operators due to Corona sick leave.
The SMART version of Piab’s renowned vacuum conveyor is pre-programmed with advanced algorithms to eliminate complex manual timer settings and allows continuous adaptive automatic fine tuning of the conveying process as well as recipe handling.
The self-optimizing conveyor system adjusts to the product to be conveyed in just ten minutes. Based on machine learning, a smooth material flow can be guaranteed under all conditions and at speeds that are precisely matched to the specific substances. Parameters can be adjusted regardless of the pipe diameter or delivery length. These adjustments are automatically checked every four seconds. The changeover is not only fast but also extremely reliable. This is made possible by the combination of sensors, an electrical control unit and intelligent software.
For usage in the pharmaceutical and food industries all material in contact with the conveyed product fulfil the requirements of FDA and EC No. 1935/2004 and designed according to USDA guidelines.
Making the best of challenging times can mean taking the COVID implied shift towards digitalization and increased technology usage that happened already in both our work and personal life one step further. By seizing the opportunity to innovate, trying out new ways of doing things and looking for the most productive solution of each process step to come out of the crisis with a more robust and competitive operational set-up. Evolving powder handling to increase productivity, free operators from straining tasks and reduce contagion and contamination risk for an ultimately safer operation can be an easy and effective starting point.