Pneumatic seals
Piab’s pneumatic seals are integral to maintaining the efficiency of the vacuum conveyors. These seals or gaskets are crucial for creating and maintaining the vacuum necessary for the pneumatic system to function effectively.
Overview of the pneumatic seal types used in Piab vacuum conveyors
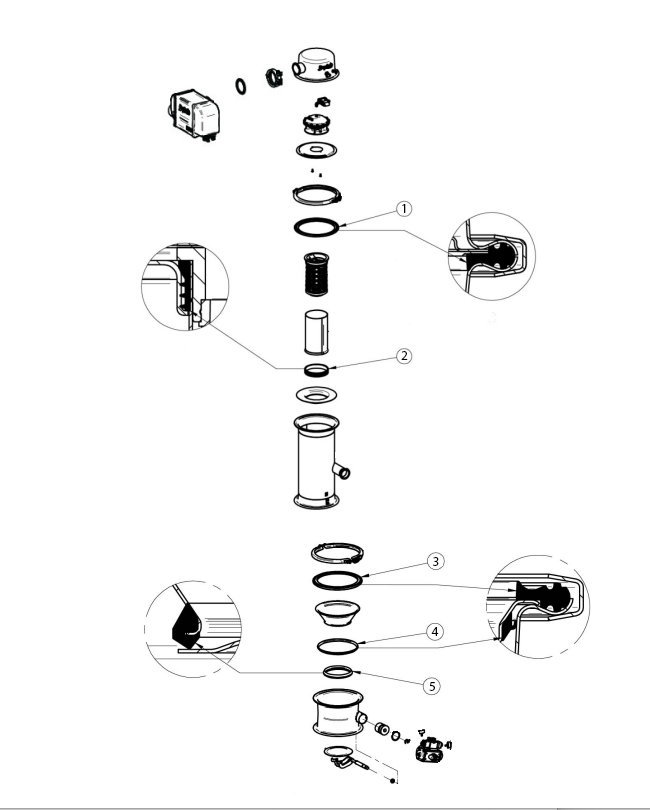
Four seal types are present in the Piab vacuum conveyor body. The (1) and (3) Module filter plate seal have two different inner edges: one side is flat, and the other one is curved. It is used on the filter plate on the top of the conveyor and at the bottom valve. When used on the filter plate, the flat side of the gasket shall be placed up. When used at the bottom valve, it ensures that the upper edge of the valve cone sits well. In this case, the flat side should be facing the bottom.
The (2) Filter seals are located around the filters and hold them in place on the filter plate. Depending on their capacity, a Piab vacuum conveyor can have 1, 3, or 7 filters.
The (4) Fluid seals/valve cone seals are thinner and smaller than others in the Piab assortment. They are located beneath the valve cone and the bottom valve and don't have direct contact with the conveyed product if used as intended. They hold the valve cone in place and force the air through the fluidization cone. Finally, the (5) Bottom valve seals sit the lowest on the conveyor, where the bottom valve swings up.
Other pneumatic seals in the Piab assortment are Module fluid seals, which are used when the feed station is fluidized. In this case, a fluid cone is installed in the feed station, and the seals help the fluid cone sit stable in the feed station. Module seals are also used in conveyor flanges. They are used in most small—to medium-sized Piab piFLOWp, piFLOWt, and piFLOWfc conveyors.
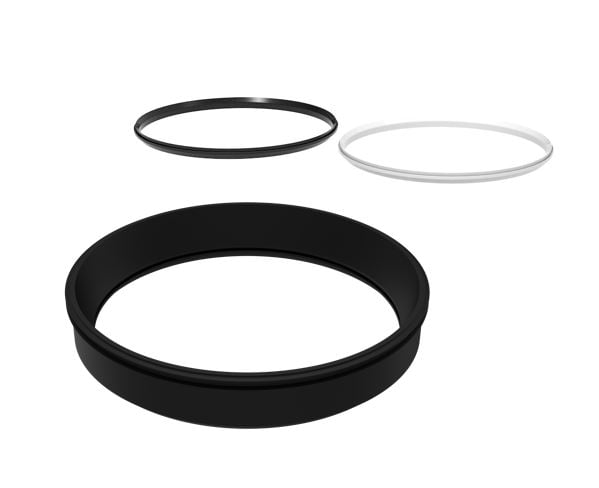
Bottom valve seals
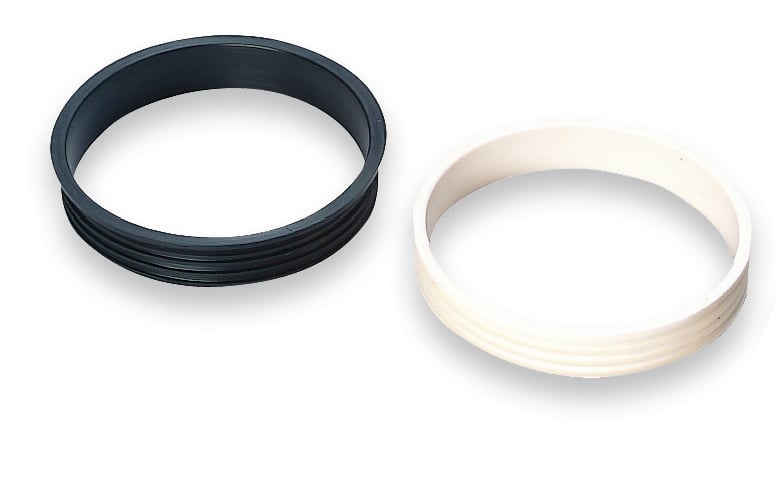
Filter seals
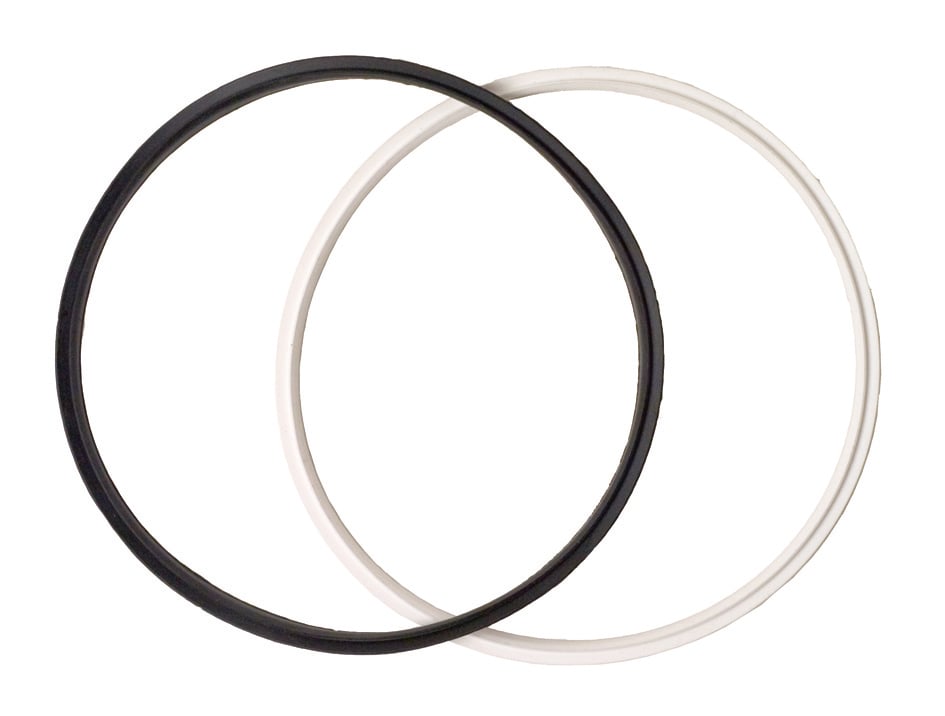
Fluid seals
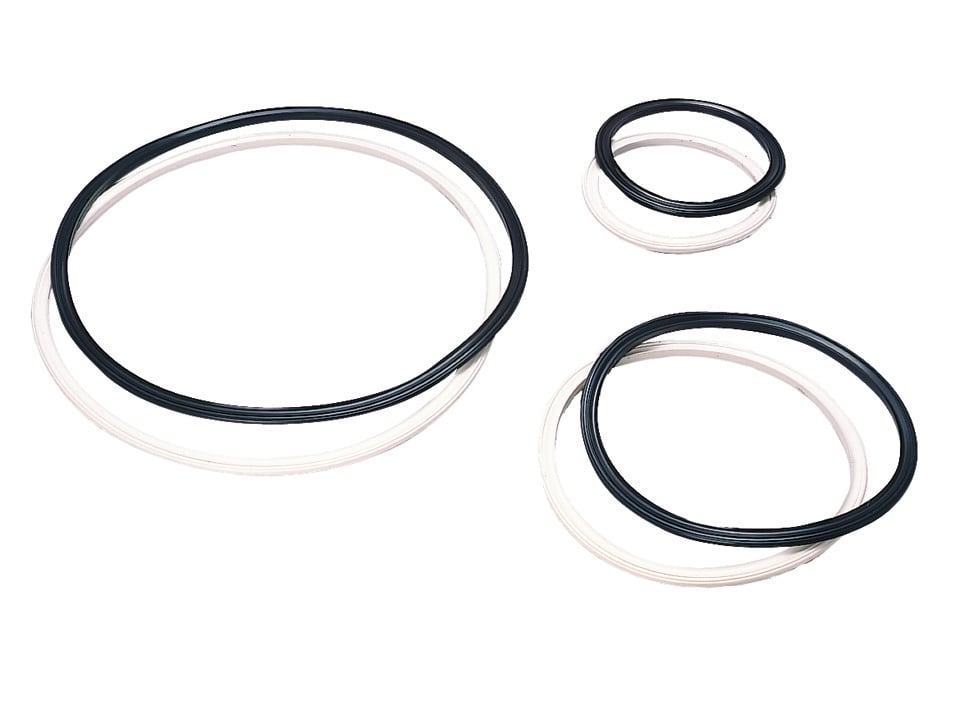
Module filter plate seals
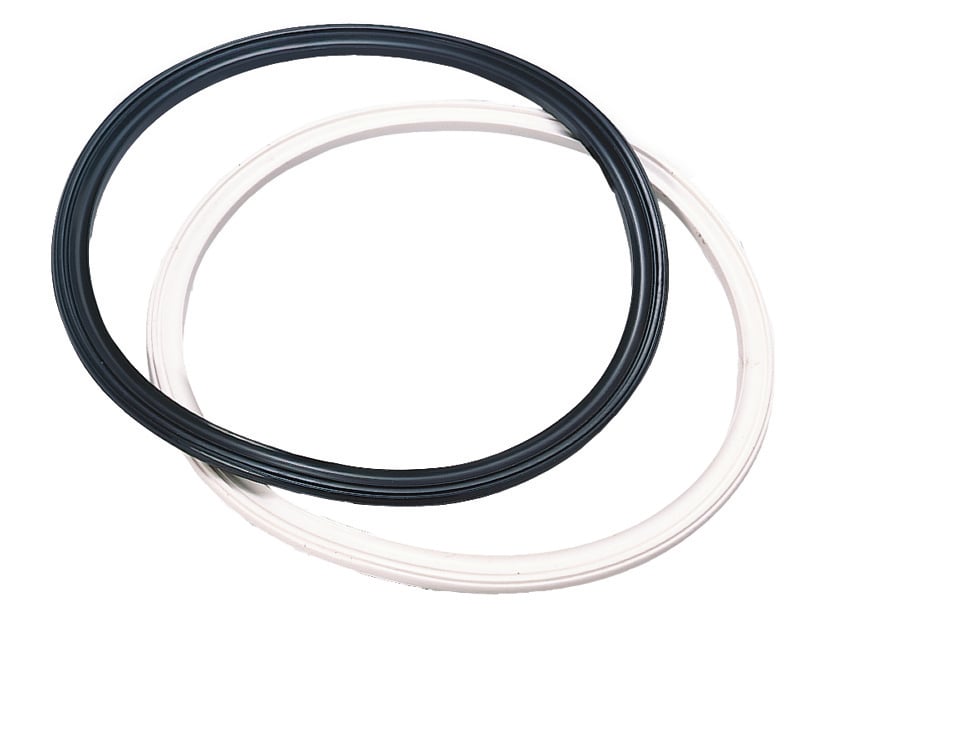
Module fluid seals
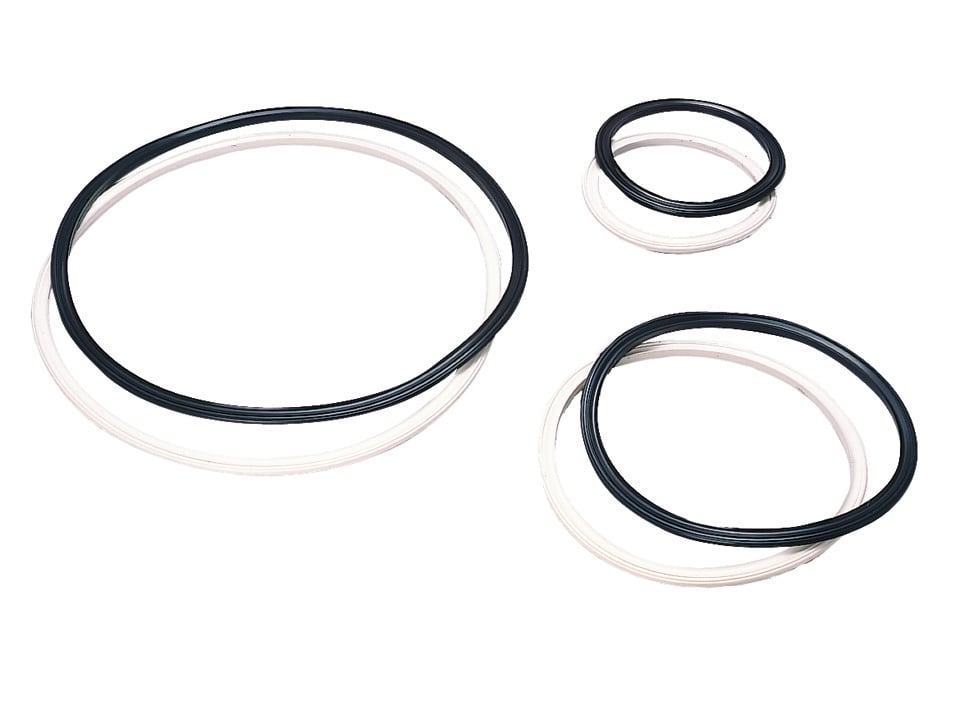
Module seals
Advantages of the Piab pneumatic seals
By ensuring a tight seal, they prevent the loss of air pressure, which is essential for the stable operation of Piab vacuum conveyors. This enhances the system’s reliability and optimizes energy consumption, leading to cost savings and environmental benefits.
The pneumatic gasket range is designed to ensure maximum compatibility and longevity of the vacuum conveyor system. These pneumatic cylinder seals are crafted from high-quality Q polymer and adhere to stringent regulatory standards, including FDA, EC No. 1935/2004, and EC No. 10/2011, ensuring they meet the highest safety and quality requirements.
The gaskets are available in two variants: white silicone seals for non-ATEX applications, and black NBR (nitrile butadiene rubber) seals, which are antistatic and ATEX certified, suitable for environments where explosive atmospheres may be present. This distinction ensures manufacturers can choose products that best fit their specific operational requirements and safety standards.
Moreover, the design of Piab’s seals contributes significantly to the hygiene and cleanliness of the conveying process. By preventing material leakage and ensuring an enclosed, dust-free system, these seals help maintain the integrity and quality of the conveyed materials. This is crucial for industries where even minor contamination can lead to significant product quality issues.
Maintenance of pneumatic seals
Pneumatic seals may be inspected for tears and hairline cuts during regular maintenance. As filters need more frequent inspections, the seals may be inspected together with the filters. When smaller imperfections appear, they need to be replaced. This is because small cuts may propagate to bigger defects due to the nature of the material.
Piab’s seals and gaskets enhance the operational efficiency of pneumatic conveyor systems and play a critical role in ensuring compliance with health and safety regulations, making them indispensable components in modern industrial applications.
Do you need help choosing the right product?
Get free advice from our engineers