
Pneumatic conveying systems by Piab
What is pneumatic conveying?
Pneumatic conveying systems are designed to use pressure differential to move bulk materials from one process area to another. Powders, granules, and many other dry bulk materials can be transferred through enclosed pipelines with the help of a pressure differential and gas or airflow.
Pneumatic conveyors work best with fine, fluidizable, dry powders that can easily “fly” through the conveying line. The systems find applications in a variety of industries, including food processing, pharmaceuticals, chemicals, or metal additive manufacturing. There is a long list of different powders that can be conveyed with pneumatic conveying, including flour, cement powder, carbon black, sugar, plastic pellets, small food particles, tablets, sands, metal powders, and many more.
Moist or heavy, granular materials, such as crushed rock, large food particles, wet sand, and gravel, are – on the other hand - not suitable for pneumatic conveying, for example, products with particle sizes larger than 30mm/1.2" and bulk densities over 8kg/l / 500 lb/ft³.
How does the pneumatic conveyor work?
Pneumatic conveyors either work with positive pressure or vacuum. With positive pressure conveying systems the material is pushed by the higher pressure on the feed side of the conveying system. Vacuum conveyors on the other hand pull the material with a vacuum that is created on the receiving side of the pneumatic conveying system.
These systems are comprised of four basic elements:
- a vacuum source,
- a material feed device,
- a conveying line and
- an air-material separator.
Cyclic operation
It generates a vacuum, and the conveyed material is transferred from the feeding point into the conveying line and then to the container.
During the conveying process, the filters protect the pump and the surrounding area from dust and small particles, and the air shock tank is filled with compressed air.
After each cycle, the bottom valve opens, and the material is discharged into a hopper or any other piece of equipment.
At the same time, the filters are cleaned with a filter shock or similar cleaning method in each cycle.
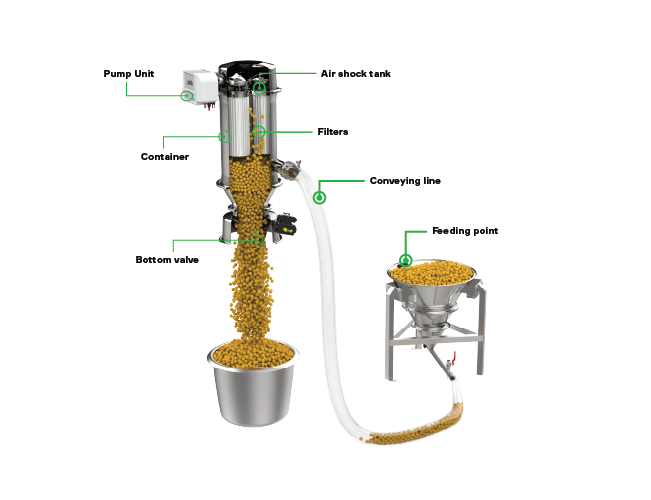
Types of pneumatic conveying systems to choose from
Dense phase pneumatic conveyor
In dense phase conveying, the material is conveyed in a more concentrated, slower-moving plug or slug within the pipeline. This method is suitable for lighter or more fragile materials, and it reduces the risk of material degradation when tablets or other small parts are transferred which are prone to chipping in the transferring process. Dense phase conveying is often used for short distances. It is important when gentle handling of the material is needed.
Medium phase pneumatic conveyor
Medium phase conveying falls between lean phase and dense phase conveying in terms of material concentration. The velocity is higher than that of dense phase conveying but lower than dilute phase conveying. Medium-phase conveying is a balance between dilute and dense phase. It provides a flexible solution for materials that fall in between these two types.
Dilute (lean) phase pneumatic conveyor
In dilute phase conveying, the material is transported in suspension within a stream of air or gas. The terms "dilute phase" and “lean phase” are thereby often used interchangeably. The material is usually moved at high speeds. The amount of material in the air is low inside the conveying line. Dilute phase or lean phase conveying is suitable for heavier materials and is often used for longer-distance transport.
How do mechanical conveyors work with bulk powders?
The basic components of a mechanical conveying system include a drive motor through a gear and/or chain reducer connected to a drive device, such as a roller or a sprocket. The motor's energy is transferred directly to the conveyor, which is in direct contact with the conveyed material. Mechanical conveyors can be open or closed to the atmosphere, with hundreds of moving and working parts.

Types of mechanical conveyors
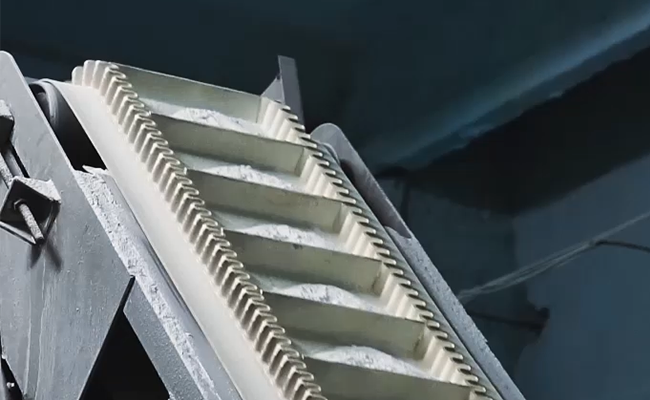
Bucket elevators
Bucket elevators have an open, uncovered top and a rotation belt. When the product material is undischarged in a cycle, then it usually disperses into the production area.
Installation of a bucket elevator requires civil engineering which is time consuming, expensive and entails high maintenance costs. It is also a rigid system which can only work on the capacity that it was planned for. It is not fulfilling the highest hygienic standards as it has big contact areas with the conveyed product, and it is also hard to sanitize it.
Belt conveyors
Belt conveyors consume a lot of floor space. These are bulky pieces of equipment that have a high risk of spillage.
Belt conveyors have high maintenance costs, especially if they are used to convey abrasive materials. Apart from spillage, sanitization is also a major issue, and the conveyed material can easily get into the air, causing health issues and the risk of dust explosions.
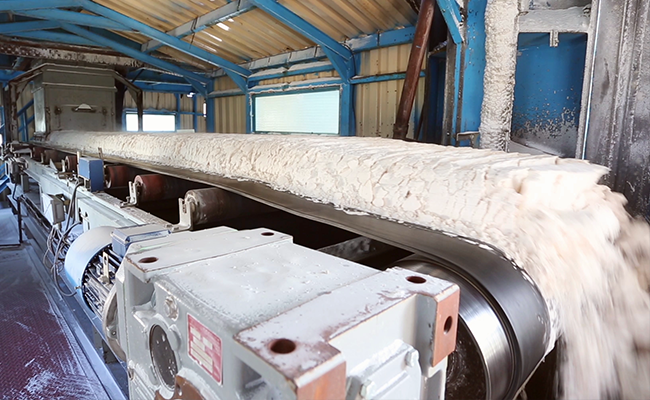
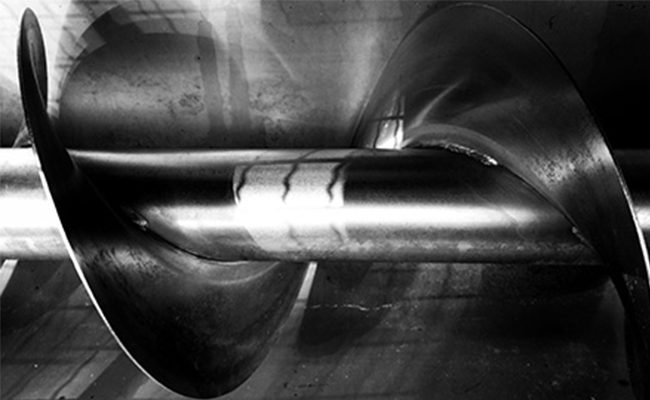
Screw conveyors
The friction caused by screw conveyors can lead to significant damage as well as temperature change in the conveyed material.
Screw conveyors don’t allow curves or direction changes, they are bulky and can’t convey in a vertical line which makes their application areas limited. They are also difficult to clean.
Why choose pneumatic conveyors with vacuum over mechanical conveyors?
The safest option to convey powders
There are no moving parts that can cut objects or need lubrication, no pinch points that could grab clothing or nip points where gears meet.
Eliminates the risk for contamination
Materials are transferred in a closed system. Unlike a belt chain conveyor, pneumatic systems contribute to a high speed continuous loop.
Saves space
Pneumatic conveyors can even be mounted right below the ceiling, taking up only a fragment of space compared to a mechanical conveyor.
Eliminiert Verschüttungen in der Produktionslinie
Die geschlossenen Rohrleitungen reduzieren die Möglichkeit von Produktverlusten erheblich.
Easy to clean and sanitize
Pneumatic conveyors usually have an in-built filter cleaning system that prevents the filters from clogging.
Flexible and easier to maintain
Switching between materials and maintenance generally takes much less time compared to mechanical conveyors.
How to choose the right conveyor type?
There are several factors affecting the selection, like:
- Material characteristics, such as particle size, distribution and shape, hardness, the tendency to get hygroscopic and fluidize, moisture content, concentration, and bulk density
- Environmental factors, such as temperature, humidity
- Connected equipment characteristics, such as system distance and throughput, height, and angles.
The most important factor is material characteristics. Pneumatic conveyors work best with fine, fluidizable, dry powders which can easily “fly” through the conveying line. There is a long list of different powders that can be conveyed with pneumatic conveying, including flour, cement powder, carbon black, sugar, plastic pellets, small food particles, tablets, sands, metal powders, and many more.
Moist or heavy, granular materials, such as crushed rock, large food particles, wet sand, and gravel, are – on the other hand - not suitable for pneumatic conveying. Humidity often affects conveying as certain materials, like sugar, become hygroscopic (sticky) in tropical climates.
The size of the conveyor, the optimal pump, pipes, and other accessories are determined by the required throughput, height, and the number of angles the pipes must have. These parameters must all be considered when the optimal way of conveying is planned, so it is extremely important to choose the right provider with extensive know-how.
The application engineers of Piab are among the most knowledgeable professionals in this area, building on 70 years of experience in industrial automation.
Get help choosing your ideal conveying equipment!
Find out what applies to your raw materials and products! Fill in the form to get free, personal advice from our engineers as well as comparisons with other technologies to find the best solution for your needs.