- Noticias
- At Nipro the piCOMPACT® provides the vacuum performance needed in production of pharma packaging made of glass
At Nipro the piCOMPACT® provides the vacuum performance needed in the production of pharma packaging made of glass
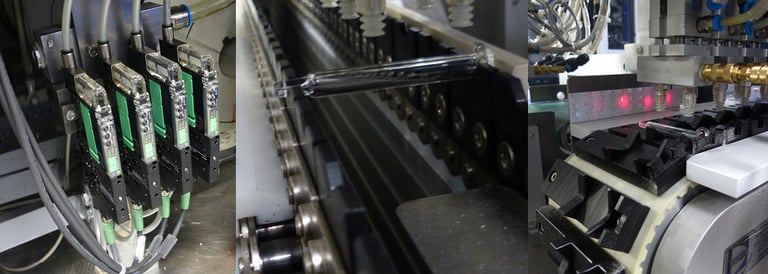
At Nipro PharmaPackaging Germany, Piab’s piCOMPACT® ejectors and silicone bellows suction cups keep production running. With 32,500 cycles per day, 24 hours a day, seven days a week, this application is one of those with the highest number of cycles per unit of time - making it the ultimate function and service life test for any vacuum ejector.
As is so often the case in the pharmaceutical sector, reliability and efficiency are key. This is also true for the manufacture of single-use glass syringes with cannulas for the packaging of, for example, insulin and thrombosis injections for home treatment.
At the company Nipro in Münnerstadt, Germany, the previously used single-stage ejectors were therefore replaced by piCOMPACT® vacuum pumps on two lines. These are based on Piab’s multi-stage COAX® vacuum technology, which minimizes energy consumption and offers a secure and quick hold due to the high initial vacuum flow. In this way, the four piCOMPACT® vacuum pumps per system at Nipro, which have been in continuous operation since February 2020, ensure significantly higher process stability and thus less waste and idle times due to machine downtimes when replacing the pumps.
In a multi-stage-ejector pump, compressed air enters the pump and is led through a system of ejector nozzles and chambers of varying sizes that act as a “pressure amplifier”. Different vacuum pressures are created at each chamber opening, due to different ejector nozzle diameters. There is also a common chamber in which the vacuum pressure is greater because of the combination of vacuum pressures in all other chambers. Atmospheric pressure outside the system rushes inward attempting to create equilibrium, generating an efficient vacuum flow.
The higher level of vacuum pressure in the common chamber causes rubber diaphragms or flap valves to close over the chamber openings. The only chamber not sealed is the first vacuum chambers where the deepest vacuum levels are attained. The mix of compressed air used to generate the low pressure and the vacuum flow exits through the exhaust. This process is completed in milliseconds and repeats continually as the vacuum level rises and falls.
Multi-stage-ejectors make optimum use of the energy stored in the compressed air through specially designed air nozzles and a series of progressively larger ejectors that allow the compressed airflow to expand in controlled stages. As a result, typical ratios for compressed air to vacuum flow are 1:3. That is every 1 cfm of compressed air results in 3 cfm of vacuum flow.
The selected ejector plays a crucial role in any robot system as it influences the system performance, speed and uptime greatly. One of the most important features is ejector efficiency. The speed (cycle time) will very much be determined by how fast the ejector can generate a safe vacuum level. If handling leaking materials with material variations (e.g. round or bend surfaces such as in in the syringes) the flow capacity at deeper vacuum levels is equally important to maintaining a high reliability. Initial flow capacity is particularly important in high speed machines to secure a tight quick grip with a bellows cup. Multistage ejector technology is 30-50% more efficient as compared to corresponding single stage ejector technology with the same energy consumption. The only “trade-off” with multistage ejector technology is a slightly longer ejector module. Using a single stage ejector, one must compensate with a larger ejector nozzle to achieve the same performance. That adds cost in terms of higher energy consumption and larger valves required. Furthermore, a higher noise level and more heat production during the process occur.
For high speed applications, such as cycle times <50-100ms, the speed of the valves has a big impact on the total cycle time. Direct operating valves will eliminate extra volume for air fill to pilot valves (typically poppet style). Direct operating valves improve MTBF (Mean Time Before Failure) since fewer moving parts are involved in the total valve construction. The power of the valve also determines the speed.
Most valves used on compact style ejectors with integrated controls are specified for 24 VDC power supply with a quite small voltage tolerance. It is not uncommon that end-users have poor control of the loads on the power supply they use. Quite often supply voltage in combination with the compressed air pressure is out of specification. In order to minimize downtime, machine-builders and robot integrators need to pay close attention to the allowed supply voltage range when selecting the unit and/or see if there are other features implemented to allow fluctuations in supply voltage. Adaptive PWM is a method that allows for supply voltage fluctuations.
"In addition, the piCOMPACT® has a much larger working range and is much less sensitive to fluctuations in compressed air than the single-stage vacuum ejectors we have used so far," adds Daniel Schmitt, Project & Plant Engineer at Nipro PharmaPackaging Germany. “This is particularly important because our production is clocked and not running continuously. The piCOMPACT® vacuum ejectors from Piab have been in operation with us for almost one and a half years except for the holidays and have driven fifteen million cycles without any problems during this time. ”
In addition, COAX® ejectors are up to twice as fast as other ejectors and deliver three times more flow than conventional vacuum ejectors with identical air consumption. The pump unit can deliver high performance even when the supply pressure is low or fluctuating. This was proven in independent comparative tests at the Fraunhofer Institute for Machine Tools and Forming Technology IWU in Dresden, Germany. These have shown that the Piab ejectors require significantly less compressed air in order to achieve the same performance compared to ejectors from other manufacturers. Accordingly, their use reduces the cost of providing compressed air.
With the latest edition of piCOMPACT®23 SMART the base energy function automatically shuts off the energy supply when vacuum is no longer needed in a sealed or semi-sealed system. The shut-off level and hysteresis (how much the vacuum level can drop before restart) is fully adjustable. The function can save up to 90–95% of compressed air usage in a lifting cycle. The energy saving system is combined with automatic level determination, a feature that automatically sets optimized energy saving shut-off and restart levels in every cycle based on actual conditions. The adaptive pulse width modulation reduces the power to the valves when they are in holding position and allows for full power when switching the valves to achieve as quick a response as possible. The adaptive part allows for fluctuating voltage without impacting functionality. Hence, the adaptive pulse width modulation significantly reduces power consumption, generates a lower temperature, increases robustness of the installation, and thereby extends the lifetime of the gripping unit.
"We are very satisfied with the change to the piCOMPACT® vacuum pumps from Piab. If you look at the total cost of ownership and take into account the significantly longer service life and the associated less downtime for the exchange, the lower scrap due to falling syringes and the lower compressed air requirement, its use over the service life is more cost-effective than the previous solution,“ Summarizes Schmitt the benefits from a financial perspective.
Want to know more? Contact us!
About Nipro Europe Group
The Nipro Europe Group Companies are part of Nipro Corporation Japan, a leading global healthcare company founded in 1954. With over 29,000 employees worldwide, Nipro serves the medical technology, pharmaceutical and pharmaceutical packaging industries.