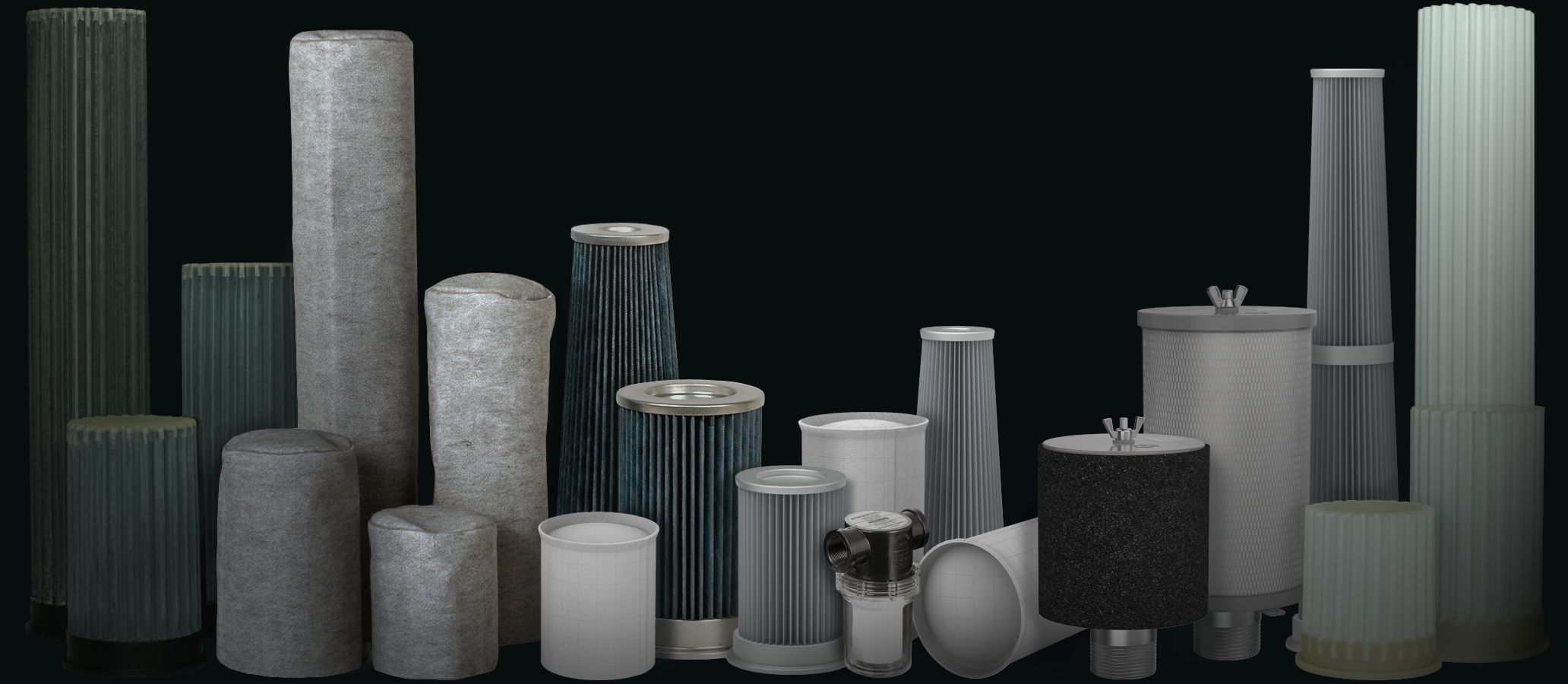
Jak wybrać odpowiednie filtry do urządzenia do transportu materiałów sypkich?
Ten artykuł jest dedykowany filtrom do urządzeń do transportu materiałów sypkich! Czytaj więcej, aby się dowiedzieć, w jaki sposób pojawiły się one na rynku we właściwym momencie ze względu na zapotrzebowanie i które parametry wpływają na ich funkcje.
Jump ahead
Filtry główne
Filtry są płucami urządzenia do transportu materiałów sypkich. Usuwają one pył, który w przeciwnym razie zanieczyściłby zakład produkcyjny i płuca operatorów. Zapewniają ponadto ciągłość działania pompy próżniowej, zgodność z rygorystycznymi i stale zmieniającymi się przepisami w zakresie bezpieczeństwa oraz innymi wymaganiami dotyczącymi BHP w ramach różnych procesów. Położenie filtrów urządzenia do transportu materiałów sypkich jest różne — mogą być one umieszczone wewnątrz korpusu przenośnika lub na zewnątrz we wlotach powietrza, aby zapewnić zgodność z wyższymi wymaganiami.
Przenośniki próżniowe stanowią hermetyczne, alternatywne rozwiązanie dla kubełkowych, śrubowych lub innych rozwiązań mechanicznych do przenoszenia proszków i granulatów. Oczekiwania i wymagania znacznie się jednak zmieniły w ciągu ostatnich dziesięcioleci. W odpowiedzi na te zmiany montaż filtrów stał się łatwiejszy, klasa filtracji i przepuszczalność powietrza zwiększyły się, a konstrukcja stała się modułowa. Seria urządzeń do transportu materiałów sypkich Piab z 1991 roku była wyposażona w jeden filtr, a obecnie jest to 1, 3 lub 7 filtrów, w zależności od przenoszonej objętości lub rozmiaru przenośnika.
Ponadto wprowadzenie wbudowanego zespołu otrzepywania ułatwiło konfigurację i czyszczenie przenośników, co doprowadziło do wydłużenia żywotności filtra i zwiększenia wydajności produkcyjnej z powodu mniejszej konieczności wykonywania sterylizacji materiału filtrującego podczas produkcji. System otrzepywania jest obecnie wbudowany w każde urządzenie do transportu materiałów sypkich Piab i jest zintegrowane z górną pokrywą przenośnika. Urządzenia te charakteryzuje praca w cyklach, a przenoszony materiał jest wyrzucany pod koniec każdego okresu do zbiornika lub maszyny odbierającej. Po zakończeniu okresu, filtr jest czyszczony za pomocą funkcji otrzepywania. Każdy filtr ma swój własny otrzepywacz, który zapewnia najwyższy poziom wydajności.
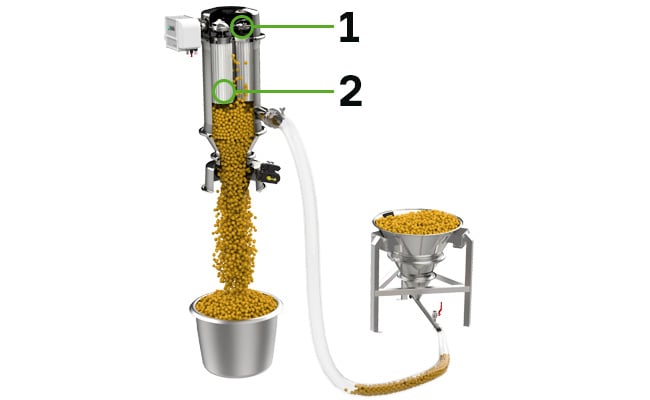
Lokalizacja filtrów wewnętrznych
W systemie transportu podciśnieniowego filtry są używane w wielu różnych miejscach. Filtry główne można znaleźć w korpusie przenośnika (2). Zapewniają one jego prawidłowe, podstawowe funkcjonowanie: gdy powietrze jest dodawane do transportowanych proszków, granulek lub małych części, musi zostać usunięte i odfiltrowane, zanim wydostanie się do otaczającej atmosfery. Czyszczenie odbywa się za pomocą funkcji otrzepywania (1).
Czyszczenie za pomocą funkcji otrzepywania
System otrzepywania składa się z jednego zbiornika na filtr, który wytwarza wstrząsy na koniec każdego cyklu transportu podciśnieniowego. Podczas pracy filtr zbiera pył po zewnętrznej stronie, gdy pompy próżniowe odciągają materiał w jego kierunku. Podczas otrzepywania dochodzi do odwrotnego procesu: powietrze jest wydmuchiwane z wnętrza filtra podczas silnego wstrząsu, co powoduje, że uwalnia on materiał.
Inne sposoby czyszczenia filtrów wewnętrznych
Większość filtrów firmy Piab można czyścić na sucho poprzez powtarzające się wstrząsy filtracyjne, a także poprzez delikatne szczotkowanie szczoteczką nieścierną lub z naturalnego, miękkiego włosia, aby uniknąć uszkodzenia membrany. Możliwe jest również czyszczenie filtrów na mokro: filtr można płukać niebezpośrednio strumieniem wody za pomocą standardowego, niskociśnieniowego węża wodnego (maks. 1 bar), bez zdejmowania go ze wspornika filtra. Po wyczyszczeniu filtr należy powiesić, aby umożliwić jego wysuszenie w pozycji otwartej. Można także zastosować metodę wet-in-place. Niektóre filtry wymagają więcej czasu na wyschnięcie po wyczyszczeniu, z powodu większej powierzchni filtrującej.
Stale rozwijamy linię filtrów i nasze urządzenia do transportu materiałów sypkich w oparciu o potrzeby naszych użytkowników. Cieszę się, że już 29 lat pracuję dla firmy, która inwestuje znaczne środki w badania i rozwój. To bardzo ciekawe doświadczenie być świadkiem ewolucji produktów Piab. Zaczynają być one coraz łatwiejsze w konfiguracji i obsłudze, a także stają się inteligentniejszymi rozwiązaniami. Modułowa budowa ułatwia skalowanie wydajności w górę i w dół oraz dostosowanie do różnych typów materiałów i przejść.
– Tomas Tiger, Globalny kierownik ds. zastosowań i dostosowywania rozwiązań
Dobieranie rozmiaru i konserwacja
Modułowość ułatwiająca konserwację
Standardowa gama filtrów Piab może odfiltrowywać małe cząstki o wielkości od 0,5 ’m już od 2000 roku. Dzięki rozwojowi produktów możliwy jest transport szerszego zakresu materiałów przy spełnieniu bardziej rygorystycznych przepisów.
Modułowość jest jednym z fundamentów rozwoju produktów w firmie Piab, co pozwala na uzyskanie wysokiego stopnia elastyczności oferowanych rozwiązań. Konserwacja filtrów jest łatwa, ponieważ są one przykręcane do korpusu przenośnika lub wciskane na płytę metalową, dzięki czemu można je szybko montować i demontować bez konieczności używania narzędzi. Niemniej jednak regularna wymiana filtrów jest nieunikniona. Dlatego zalecamy, aby zawsze uzupełniać części zamienne. Gdy jednak elementy zamienne nie są dostępne, firma Piab zazwyczaj wysyła najczęściej wykorzystywane części, takie jak filtry, w ciągu dziesięciu dni. Obowiązują przy tym lokalne zasady i warunki. Należy się skonsultować z najbliższym przedstawicielem lub partnerem firmy Piab.
Częstotliwość wymiany filtra zależy od branży, transportowanych materiałów, wydajności i innych czynników. Na przykład z reguły szacuje się, że w przemyśle farmaceutycznym filtry powinny być wymieniane co 6 miesięcy, ponieważ urządzenia są stosunkowo często czyszczone i sterylizowane. Takie częste okresy wymiany występują również w przypadku przenoszenia ceramiki ze względu na erozyjne właściwości tego materiału. Należy wtedy zastosować krótsze filtry, aby zminimalizować kontakt pomiędzy nimi, a materiałem przychodzącym. W innych przypadkach żywotność filtra może być znacznie dłuższa, a częstotliwość wymiany zależy od przenoszonego materiału, wydajności systemu, typu filtra, a nawet czynników środowiskowych, więc nie ma jednoznacznych zaleceń obowiązujących we wszystkich zastosowaniach. Zalecamy wymianę filtrów średnio raz w roku.
Co należy wziąć pod uwagę przy wyborze filtrów?
Podczas wyboru filtra do danego zastosowania należy uwzględnić kilka czynników.
Wielkość cząstek jest ważna, ponieważ drobniejsze proszki wymagają większego obszaru filtrowania, aby zapewnić maksymalną zdolność przenoszenia. Należy także wziąć pod uwagę, jak rygorystycznych zasad należy przestrzegać.
Materiały higroskopijne są często lepkie, a ich zawartość tłuszczu wynosi ponad 25%. Ponadto wyższy poziom wilgotności zwiększa właściwości higroskopijne — na przykład ma to miejsce w przypadku cukru przechowywanego w wilgotnym środowisku, takim jak kraje tropikalne. Zasadniczo jeśli możemy zrobić dłońmi śnieżkę z materiału, można go uznać za zbrylający lub zawieszający się, który tworzy mosty podczas pracy urządzeń. Ogólnie rzecz biorąc, im mniejszy i gładszy obszar filtra, tym łatwiej jest transportować materiały zawieszające się, ponieważ mają one mniej możliwości przywierania do jego powierzchni.
Z drugiej strony mniejszy obszar filtra może powodować spadek ciśnienia wokół niego, co prowadzi do zmniejszenia zdolności przenoszenia. Spadek ciśnienia jest kompensowany przez wyższą przepuszczalność powietrza materiału filtracyjnego i łatwy sposób czyszczenia za pomocą funkcji otrzepywania filtra.
Podejmując decyzję o wyborze filtra, oprócz charakterystyki materiału należy także wziąć pod uwagę rury. Pojemność pompy i filtry muszą być dostosowane do długości rury. Im dłuższa odległość przenoszenia (i długość rury), tym większa pompa musi być stosowana do transportu tej samej ilości proszku. Konieczność uzyskania wyższej wydajności oznacza, że potrzebna jest rura o większej średnicy. Na decyzję wpływa ponadto liczba zagięć rury.
Jednostki filtrujące drugiego stopnia z filtrem ULPA
Gdy przenoszone są materiały niebezpieczne, filtry można uzupełnić o jednostki filtrujące drugiego stopnia, które są skuteczne nawet w przypadku bardzo małych cząstek o wielkości od 0,2 µm. Ponieważ te jednostki filtrujące drugiego stopnia są wyposażone w filtry ULPA, są odpowiednie do szczególnie delikatnych produktów. Umieszcza się je między korpusem przenośnika a pompą.
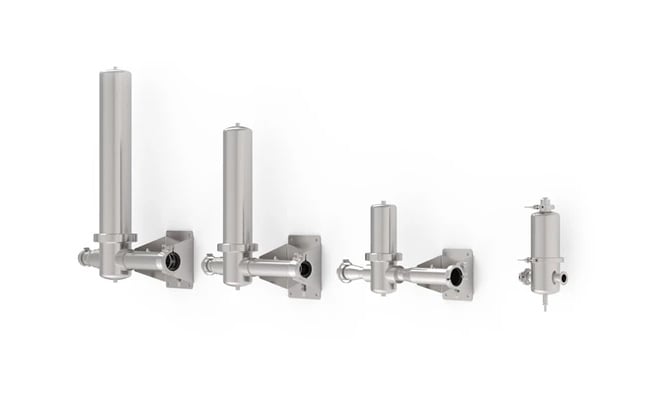
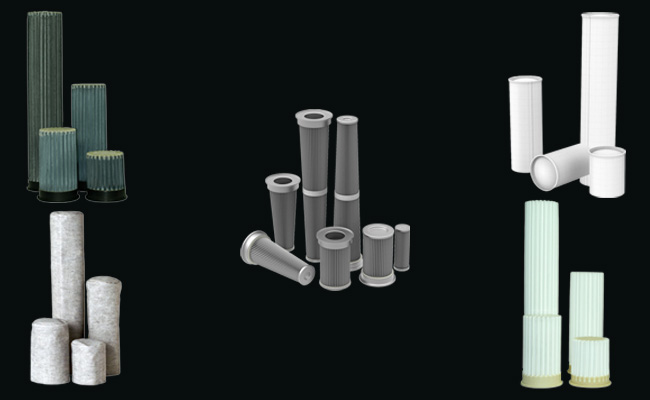
Przegląd głównych typów filtrów firmy Piab
W korpusie przenośnika umieszczane są filtry tekstylne, rurowe filtry harmonijkowe, filtry z fałdowanej stali nierdzewnej i filtry harmonijkowe. Filtry wewnętrzne firmy Piab zostały zaprojektowane tak, aby zapewniać jednocześnie maksymalne bezpieczeństwo i wydajność, dzięki czemu na linii produkcyjnej można oddychać bez obaw. Kliknij tutaj, aby wyświetlić zestawienie filtrów głównych z tabelą porównawczą:
Filtry wlotu powietrza
Filtry wlotu powietrza zapobiegają przedostawaniu się pyłu i cząstek z powietrza atmosferycznego i przenoszonego ich przez niego do systemu transportowego poprzez regulowane wloty powietrza modułu oddolnego ssania, co skutkuje ograniczonym transportem materiału przez system. Jednocześnie zapobiegają one wydostawaniu się przenoszonego materiału z regulowanych wlotów powietrza modułów oddolnego ssania, np. podczas fluidyzacji. Gdy moduł oddolnego ssania firmy Piab zostaje wyposażony w filtr wlotu powietrza, zapobiega to zanieczyszczeniu krzyżowemu. Filtry te są kompatybilne ze wszystkimi typami modułów oddolnego ssania Piab. Ponadto są zalecane, gdy w konfiguracji transportu podciśnieniowego używane są otwory wentylacyjne. Filtry wlotu powietrza są wyposażone w okap, który wydłuża ich żywotność.
Umieszczenie filtrów wlotu powietrza
W tym przykładzie zastosowania materiał jest przenoszony z beczki (1) za pomocą lancy podającej (2) do sita (3), a następnie do mieszalnika V (7) poprzez użycie węża (6) i przechodzi dalej do silosu (10), podczas gdy urządzenie do transportu materiałów sypkich znajduje się na górze (9). Filtry wlotu powietrza (5) umieszcza się na wlotach powietrza (4) modułów oddolnego ssania. Gdy filtr wlotu powietrza jest podłączony do modułów oddolnego ssania, należy zastosować specjalny reduktor (8). Tabele porównawcze są dostępne w odpowiednich instrukcjach filtrów wlotu powietrza, dzięki czemu można wybrać właściwe elementy do konfiguracji. W przypadku wszystkich typów i rozmiarów filtrów wlotu powietrza dostępne są elementy zamienne.
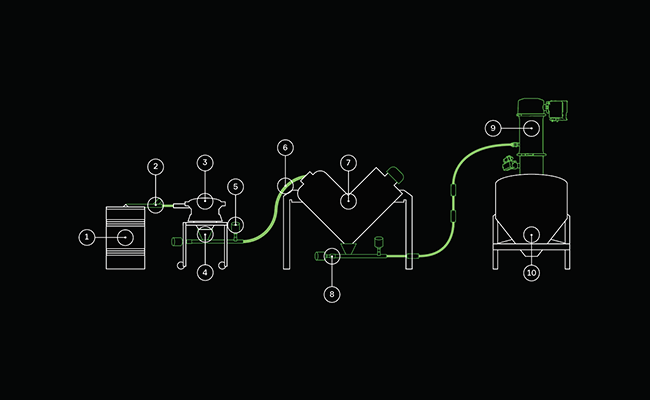
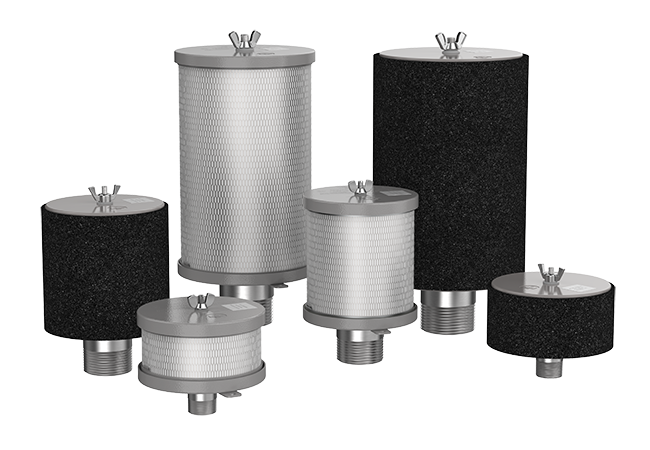
Wybierz odpowiedni filtr wlotu powietrza
Należy wziąć pod uwagę wymagany poziom zgodności z przepisami w zakładzie. Standardowy filtr wlotu powietrza (stal węglowa) jest zalecany, gdy wymagania są niższe, a przenoszone materiały są nieprzewodzące. W przypadku wyższych wymagań, takich jak właściwości antystatyczne, lub gdy niezbędna jest odporność na kwas/korozję, zaleca się stosowanie antystatycznego filtra wlotu powietrza (SS316).
Jak używać filtrów podciśnieniowych?
The so-called vacuum filters (2) are recommended when there are lower hygienic requirements in the facility and no food requirements or antistatic properties are needed. They are lightweight, made of plastic, and have a filter grade of 5-10 µm.
They may be used where extra venting is required (due to material characteristics or the process setup). One example is to cover the venting hole on transition pieces (3) under the conveyor body (1) when the material is emptied into a silo/hopper (4) or other equipment. In this case, venting is needed to ensure a smoother material transition as the vent evens the pressure.
Aby uzyskać szczegółowe dane
techniczne, należy kliknąć tutaj
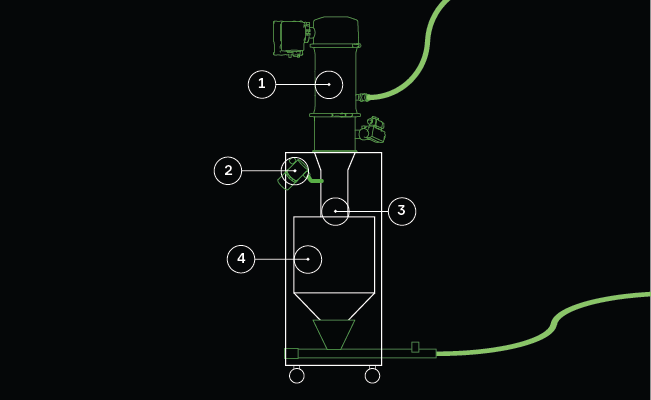