
Battery Manufacturing
Advanced handling solutions ranging from raw material conveying to later process steps like stacking, final unit assembly, and beyond, are all parts of Piab’s advanced offering for battery and fuel cell manufacturing. We provide a wide range of standardized products with proven durability as well as fully customized tools.
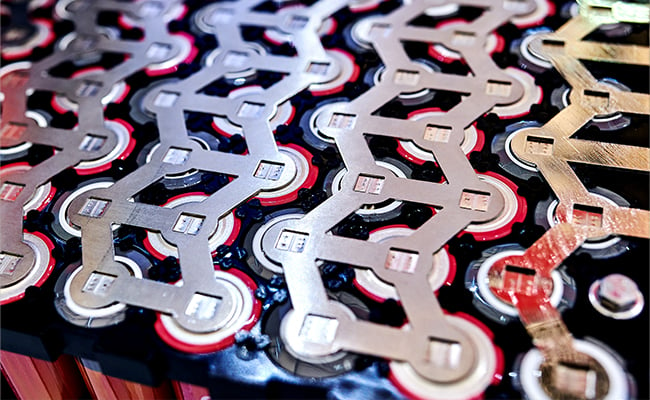
Challenges of the battery manufacturing industry
The battery manufacturing industry plays an important role in meeting the growing global demand for the automotive industry but also energy storage solutions. However, this industry is not without its challenges. From raw material shortages over handling hazardous materials to technological barriers, battery manufacturers face multiple obstacles that demand strategic and innovative solutions.
Battery manufacturing: A growing market with high demands
Battery manufacturing is one of the fastest growing markets and is still continuously evolving, driven by the need for higher energy density, longer lifespan, faster charging and improved safety. Battery manufacturers must adapt to new regulations, changing conditions and technical novelties in order to remain competitive and meet the changing needs of consumers.
Manufacturers must also find ways to scale production efficiently, optimize material costs and improve manufacturing processes to reduce prices.
With the increasing demand for electric vehicles and renewable energy systems, battery manufacturers face the challenge of scaling production rapidly to meet this growing demand. Building and expanding battery manufacturing capacity while maintaining efficiency and quality are significant challenges. To stay competitive and increase battery sales, cost reduction remains also a key challenge.
By using Piab's technology, battery manufacturers can produce with high capacity and reduce material loss and costs.
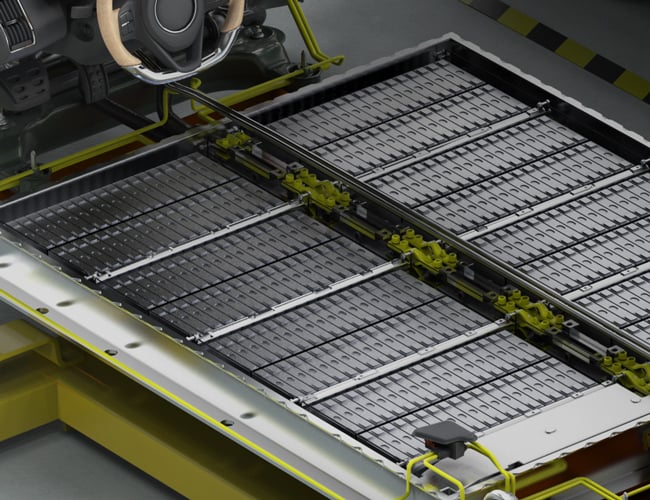
Battery handling systems: Efficiency through automation
Piab’s automation technology enables safe handling solutions even for high-speed applications for all initial stages of battery and fuel cell production, starting with handling of fragile and precious components until heavy handling of battery packs.
We provide precise battery and fuel cell handling solutions, creating quality improvements, while also reducing product waste and overall costs.
Using products ranging from energy-saving vacuum ejectors to suction cups with high durability, a true high-precision battery manufacturing process can be achieved.
Battery production process: Ensuring safety and high output with vacuum conveying
Vacuum conveying technology is used to transport and handle battery materials with care. Piab’s closed loop systems therefore help to manage transferring various battery components, especially the active materials used in the electrodes, solid state electrolytes, and other powdered ingredients. The use of vacuum conveying ensures the protection of work environments and employees by preventing cross-contamination of these battery materials.
By using Piab’s technology battery manufacturers enable a more efficient and dust-free material handling process.
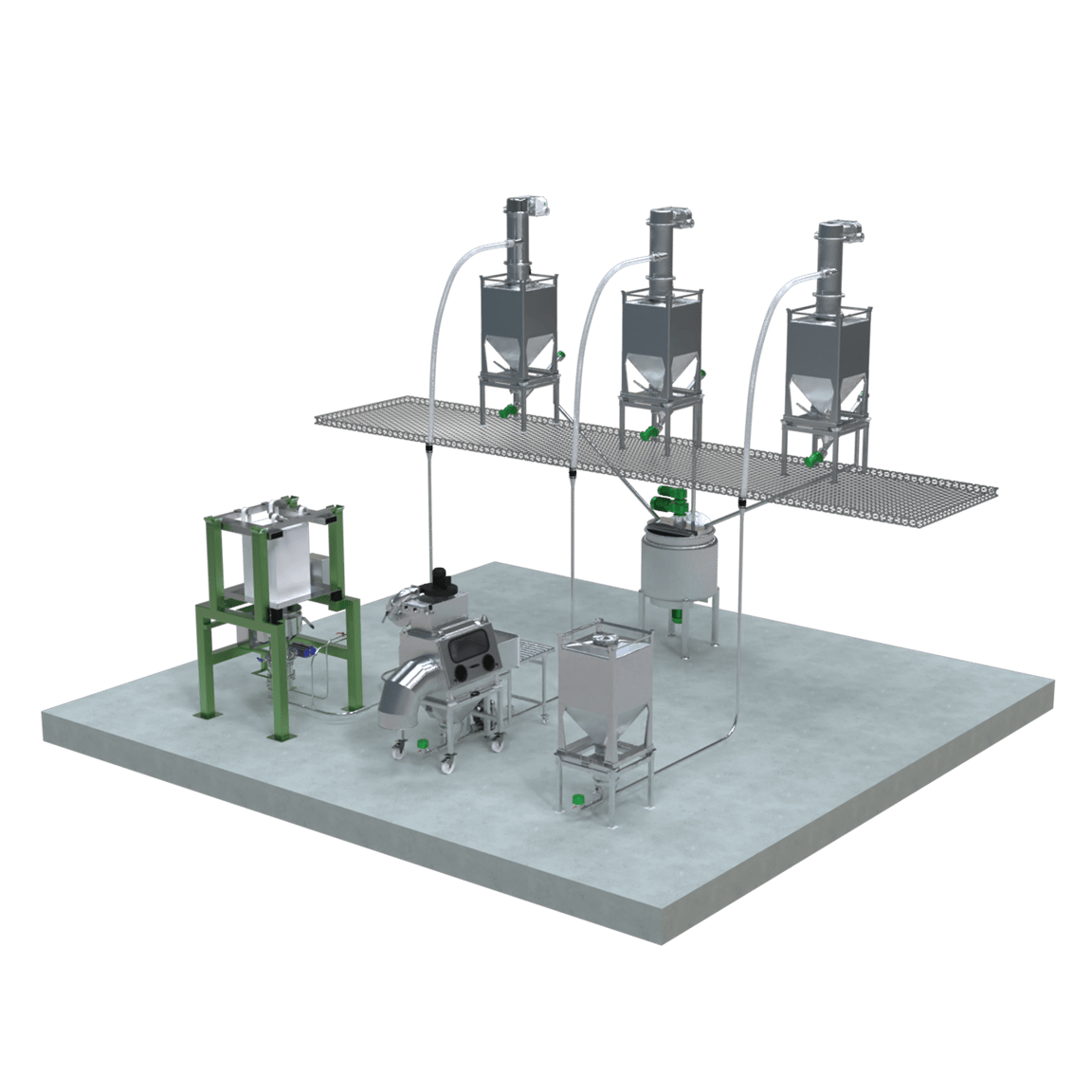
FAQ
How are batteries manufactured?
Lithium-ion battery manufacturing involves coating electrode materials onto substrates, assembling electrodes with a separator into a cell, filling it with electrolyte, and sealing it. The battery goes through a formation with initial charge cycles, followed by rigorous testing for performance and safety. The cells are then assembled into modules and than stacked to a battery stack, which will then go into the battery pack. After packaging for distribution, the batteries can be used in electric vehicles, consumer electronics and other applications. This process emphasizes quality control and safety to ensure reliable battery performance.
What are the main benefits of automation in battery manufacturing?
Automation in battery manufacturing offers several key benefits, including increased production efficiency and consistency, which leads to higher quality products and reduced manufacturing costs. It enhances precision and reduces human errors, ensuring consistent performance and reliability of batteries. Additionally, automation improves safety by minimizing human exposure to hazardous materials and processes. It also enables scalability, allowing manufacturers to quickly adapt to changing market demands and technological advancements. Overall, automation in battery manufacturing drives innovation, cost-effectiveness, and competitiveness in the industry.
What are the key challenges in scaling up battery manufacturing production?
Scaling up battery manufacturing production involves several key challenges, including maintaining consistent quality, managing supply chain complexities, and ensuring cost efficiency. As production volumes increase, it becomes crucial to maintain the same high standards of quality control to avoid defects and ensure product reliability. Supply chain management also becomes more complex, requiring efficient coordination of raw materials, components, and logistics to meet production schedules. Additionally, manufacturers must find ways to optimize production processes to reduce costs while scaling up, which often involves investing in advanced automation technologies and improving operational efficiencies. Addressing these challenges is essential for meeting the growing demand for batteries in various applications, from electric vehicles to renewable energy storage.