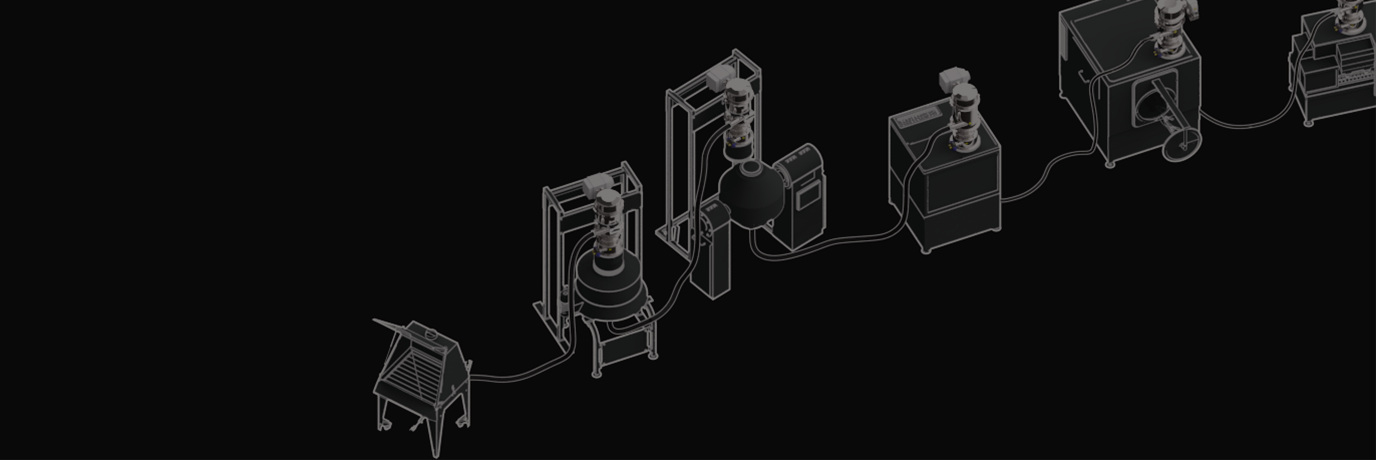
Pneumatic conveying systems by Piab
Introducing future-oriented pneumatic solutions for efficient material handling. Piab designs conveying systems to meet the evolving needs of modern industries. These systems use air pressure to move materials quickly and efficiently. This makes them a great choice for many industries, including food processing, battery production, additive manufacturing, and pharmaceuticals.
What is pneumatic conveying?
Pneumatic conveying systems use pressure differential to move bulk materials from one process area to another. You can move powders, granules, and other dry bulk materials through closed pipelines. You achieve this using a pressure difference and gas or airflow.
Pneumatic conveyors work best with fine, fluidizable, dry powders that can easily “fly” through the conveying line. The systems find specific applications in a variety of industries. Many different powders can be moved using pneumatic conveying. These include flour, cement powder, carbon black, carbon steel, sugar, and plastic pellets. It also works for small food particles, tablets, fine sands, metal powders, excipients and APIs, and more.
Moist or heavy materials, like crushed rock, large food pieces, wet sand, and gravel, are not suitable for pneumatic conveying. This includes a range of materials with particle sizes larger than 30mm or 1.2 inches and bulk densities over 8kg/l / 500 lb/ft³.
Pneumatic conveying system working principle
Pneumatic conveyors either work with positive pressure or vacuum.
In positive pressure conveying systems, the material is pushed by higher pressure on the feed side. Vacuum conveyors, on the other hand, use a vacuum to pull the material. This vacuum is created on the receiving side of the pneumatic conveying system.
These systems are comprised of four basic elements:
- a vacuum source,
- a material feed device,
- a conveying line and
- an air-material separator.
Cyclic operation in a pneumatic conveyor
The pump unit creates a vacuum. The material moves from the feeding point into the conveying line and then to the container.
During the conveying process, the filters keep the pump and nearby area safe from dust and small particles.
After each cycle, the bottom valve opens. The material is then released into a hopper or other equipment.
At the same time, the filters are cleaned with a filter shock from the air shock tank in each cycle.
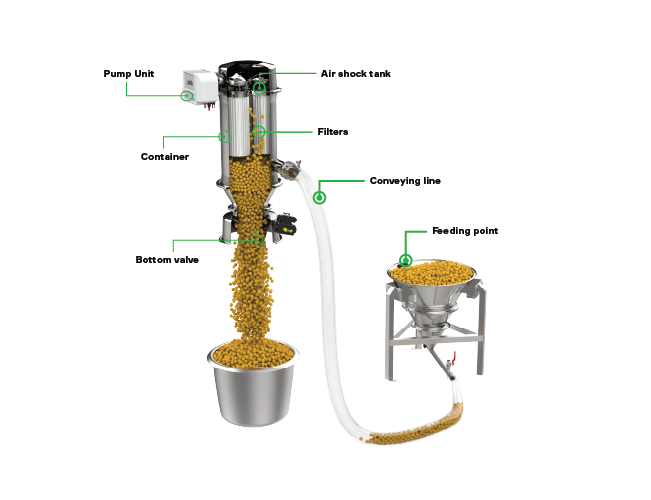
There are 3 types of pneumatic conveyors
Dense phase pneumatic conveyor
In dense phase conveying, the material is conveyed in a more concentrated, slower-moving plug or slug within the pipeline. This method is suitable for lighter or more fragile materials, and it reduces the risk of material degradation when tablets or other small parts are transferred which are prone to chipping in the transferring process. Dense phase conveying is often used for short distances. It is important when gentle handling of the material is needed.
Medium phase pneumatic conveyor
Medium phase conveying falls between lean phase and dense phase conveying in terms of material concentration. The velocity is higher than that of dense phase conveying but lower than dilute phase conveying. Medium-phase conveying is a balance between dilute and dense phase. It provides a flexible solution for materials that fall in between these two types.
Dilute (lean) phase pneumatic conveyor
In dilute phase conveying, the material is transported in suspension within a stream of air or gas. The terms "dilute phase" and “lean phase” are thereby often used interchangeably. The material is usually moved at high speeds. The amount of material in the air is low inside the conveying line. Dilute phase or lean phase conveying is suitable for heavier materials and is often used for longer-distance transport.
Different types of conveyor systems: pneumatic vs mechanical
The main parts of a mechanical conveying system include a drive motor. This motor connects to a gear or chain reducer. The reducer is linked to a drive device, like a roller or a sprocket. The motor's energy is transferred directly to the conveyor, which is in direct contact with the conveyed material. Mechanical conveyors can be open or closed to the atmosphere, with hundreds of moving parts.
Why mechanical conveyors aren't suitable for bulk powder and granule transfer?
Mechanical conveyors (conveyor belts, bucket elevator conveyor, and screw auger conveyor) work well in the material flow of many products. However, they aren't suitable to move products that require gentle handling, such as bulk powders and granules.
One of the primary reasons to prefer pneumatic conveyor systems to a mechanical one is to preserve materials from degradation or compaction. Mechanical systems, such as belt or screw conveyors, can exert excessive pressure on delicate powders, leading to clumping or even damage to the material's structure.
Mechanical conveyors can struggle with the uniformity of the assembly line and present the potential for dust generation. Moreover, drag chain conveyors often require more maintenance due to wear and tear from moving parts. In contrast, pneumatic systems typically have fewer moving components, which can lead to lower maintenance costs and an increased reliability.
Types of mechanical conveyors
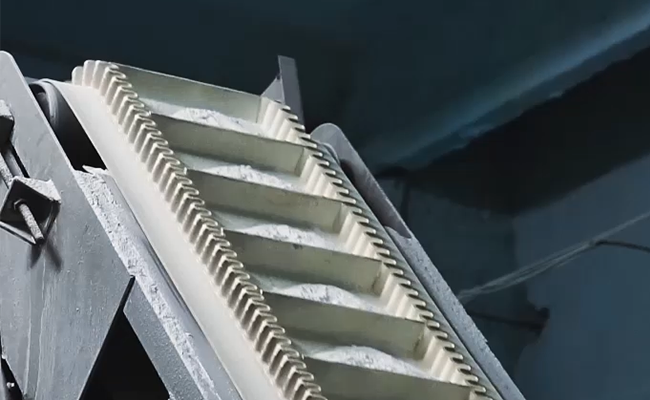
Bucket elevators
Bucket elevators have an open, uncovered top and a rotation belt. When the product material is undischarged in a cycle, then it usually disperses into the production area.
Installation of a bucket elevator requires civil engineering which is time-consuming, expensive and entails high maintenance costs in designing and manufacturing. It is also a rigid system that can only operate within the capacity for which its planners designed it. The elevator bucket does not meet the highest hygiene standards. It has large contact areas with the product, making it hard to clean.
Belt conveyors
Belt conveyors consume a lot of floor space. These are bulky pieces of equipment that have the highest risk of spillage among all conveyor chains.
Belt conveyors incur high maintenance costs, especially when users employ them to convey abrasive materials. Besides spillage, cleaning is also a big concern. The material can easily enter the air. This can lead to health problems and the risk of dust explosions.
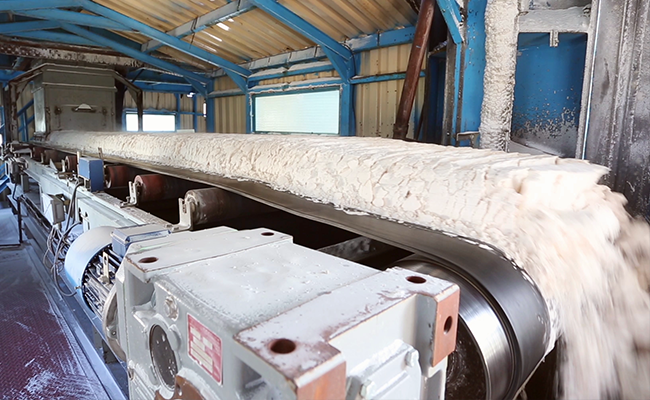
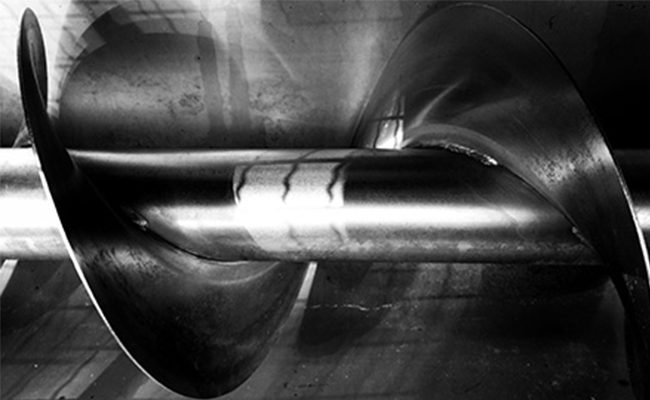
Screw conveyors
Screw conveyors can cause serious damage and change the temperature of the material they move due to friction. There is also a risk that the material slides back down the tube if very fine powders like synthetic graphite are conveyed.
Screw conveyors cannot have curves or change direction. They are bulky and cannot move materials vertically. This limits where they can be used. Besides being not flexible, screw conveyor is also difficult to clean.
Choose pneumatic conveyors with vacuum over mechanical conveyors
The safest option to convey powders
There are no moving parts that can cut objects or need lubrication, no pinch points that could grab clothing or nip points where gears meet.
Eliminates the risk for contamination
Materials are transferred in a closed system. Unlike a belt chain conveyor, pneumatic systems contribute to a high speed continuous loop.
Saves space
Pneumatic conveyors can be installed just below the ceiling. They occupy much less space than mechanical conveyors.
Eliminates spills in the production line
The closed pipelines greatly reduce the possibility of material loss.
Easy to clean and sanitize
Pneumatic conveyors usually have an in-built filter cleaning system that prevents the filters from clogging.
Flexible and easier to maintain
Switching between materials and maintenance generally takes less time compared to mechanical conveyors.
How to choose the right conveyor type?
Several factors affect the selection, such as:
- Material characteristics, such as particle size, distribution and shape, hardness, the tendency to get hygroscopic and fluidize, moisture content, concentration, and bulk density
- Environmental factors, such as temperature, humidity
- Connected equipment characteristics, such as system distance and throughput, height, and angles.
Revise material characteristics
The most important factor is material characteristics. Pneumatic conveyors work best with fine, fluidizable, dry powders which can easily “fly” through the conveying line. Do you have to move a powder with high bulk density? Many different powders can be moved using pneumatic conveying. These include flour, cement powder, carbon black, sugar, and plastic pellets. It also works for small food particles, tablets, sands, metal powders, and more.
Check equipment characteristics
The size of the conveyor, the best pump, pipes, and other parts depend on the needed throughput. They also depend on the height and the number of angles in the pipes. All these factors must be considered when planning the best way to move the powders, granules, and small parts. It is very important to choose the right provider with sufficient expertise and proven record of successful use cases.
Consider working environment
Humidity often affects conveying as certain materials, like sugar, become hygroscopic (sticky) in tropical climates. Some spaces may have special requirements, like clean rooms in pharmaceutical manufacturing where making sure that cross-contamination is avoided is extra important.
Pneumatic conveying systems for different industries
Can't choose the right conveying equipment?
Find out what works best for your raw materials and products! Fill out the form and get a free, individual consultation from our top engineers.
We can help you find the best solution for your conveying needs.